Preventing H-beam surface corrosion is an important measure to ensure its long-term performance and safety. The following are some effective methods to prevent H-beam surface corrosion:
1. Hot-dip galvanizing
Hot-dip galvanizing is an effective anti-corrosion method. H-beam is immersed in molten zinc liquid to form a dense zinc layer on the surface of the steel. The zinc layer can effectively prevent steel corrosion and has a long service life.
2. Spraying anti-corrosion paint
Spraying anti-corrosion paint is a common method. You can choose a suitable anti-rust paint to form a protective film on the surface of the H-beam to prevent oxygen and moisture from contacting the steel, thereby playing an anti-corrosion role. Before painting, the surface of the H-beam needs to be cleaned to ensure that the paint layer can adhere well. Applying anti-corrosion paint on the surface of the H-beam effectively isolates the steel from contact with the outside air and water, and prevents oxidation of the steel surface.
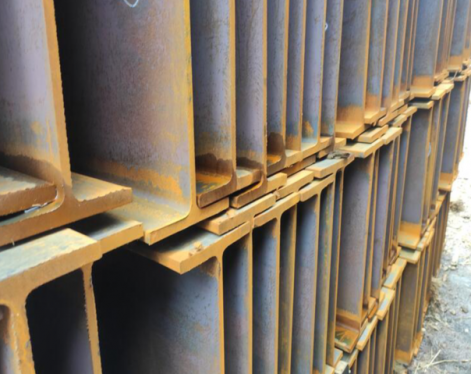
3. Anodic protection
By installing an anode protector on the surface of the H-beam, under the action of external current, cathodic protection is formed to reduce steel corrosion.
4. Cold galvanizing
Immerse the H-beam in chemical galvanizing solution to form a zinc coating on the steel surface through chemical reaction.
5. Sandblasting and rust removal
Remove the corrosion and oxides from the surface of the H-beam by high-pressure sandblasting machine, and then apply anti-corrosion paint to block the contact between the steel and the environment.
6. Thermal spraying
Spray molten metal or alloy on the surface of the H-beam to form a firmly attached metal coating to play an anti-corrosion role.
In addition, the spraying method can also be used. The plastic powder is attached to the surface of the H-beam by electrostatic spraying to form a plastic protective layer. This method can not only prevent corrosion, but also play a certain decorative role.
These anti-corrosion technologies can be used alone or in combination to achieve better anti-corrosion effects. Different anti-corrosion treatment methods have their own advantages and disadvantages. According to the specific use environment and requirements, you can choose a suitable anti-corrosion method.
H-beam anti-corrosion precautions:
1. Use environment
Choose a suitable installation location: During the design stage, the use environment of H-beam should be taken into consideration, and it should be avoided as much as possible in areas with high corrosion risks, such as coastal areas, industrial areas, etc.
Environmental improvement measures: For unavoidable harsh environments, ventilation and drainage facilities can be added to reduce the accumulation of corrosive media. At the same time, regular cleaning of the surface of H-beam and removal of attached corrosive substances are also effective preventive measures.
2. Strengthen maintenance and inspection
Regular inspection: Regularly inspect H-beams and observe the state of their surface coating or plating. Once the coating is found to be damaged or aged, it should be repaired or repainted in time to ensure the integrity of the protective layer.
Maintenance management: Strengthen the maintenance and management of H-beams, including regular cleaning, rust removal and repainting. At the same time, for parts that are difficult to paint, such as welds, bolted joints, etc., sacrificial anode protection or sealant filling can be used to enhance local corrosion resistance.
3. Other measures
Avoid the use of corrosive chemicals: During installation and use, chemicals that may cause corrosion, such as acidic cleaners, should be avoided. At the same time, for accessories such as fasteners, corrosion-resistant materials should also be selected to reduce corrosion sources.
Reasonable storage and transportation: When storing and transporting H-beams, care should be taken to avoid contact with corrosive substances, and try to maintain a dry and ventilated environment to reduce the risk of corrosion.
1. Hot-dip galvanizing
Hot-dip galvanizing is an effective anti-corrosion method. H-beam is immersed in molten zinc liquid to form a dense zinc layer on the surface of the steel. The zinc layer can effectively prevent steel corrosion and has a long service life.
2. Spraying anti-corrosion paint
Spraying anti-corrosion paint is a common method. You can choose a suitable anti-rust paint to form a protective film on the surface of the H-beam to prevent oxygen and moisture from contacting the steel, thereby playing an anti-corrosion role. Before painting, the surface of the H-beam needs to be cleaned to ensure that the paint layer can adhere well. Applying anti-corrosion paint on the surface of the H-beam effectively isolates the steel from contact with the outside air and water, and prevents oxidation of the steel surface.
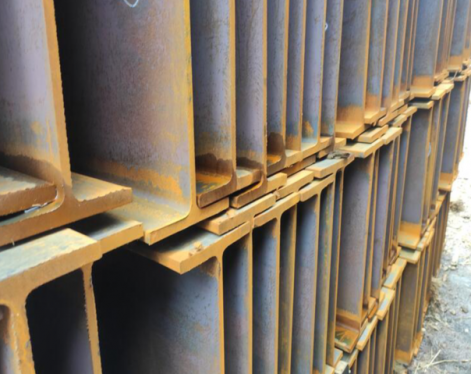
3. Anodic protection
By installing an anode protector on the surface of the H-beam, under the action of external current, cathodic protection is formed to reduce steel corrosion.
4. Cold galvanizing
Immerse the H-beam in chemical galvanizing solution to form a zinc coating on the steel surface through chemical reaction.
5. Sandblasting and rust removal
Remove the corrosion and oxides from the surface of the H-beam by high-pressure sandblasting machine, and then apply anti-corrosion paint to block the contact between the steel and the environment.
6. Thermal spraying
Spray molten metal or alloy on the surface of the H-beam to form a firmly attached metal coating to play an anti-corrosion role.
In addition, the spraying method can also be used. The plastic powder is attached to the surface of the H-beam by electrostatic spraying to form a plastic protective layer. This method can not only prevent corrosion, but also play a certain decorative role.
These anti-corrosion technologies can be used alone or in combination to achieve better anti-corrosion effects. Different anti-corrosion treatment methods have their own advantages and disadvantages. According to the specific use environment and requirements, you can choose a suitable anti-corrosion method.
H-beam anti-corrosion precautions:
1. Use environment
Choose a suitable installation location: During the design stage, the use environment of H-beam should be taken into consideration, and it should be avoided as much as possible in areas with high corrosion risks, such as coastal areas, industrial areas, etc.
Environmental improvement measures: For unavoidable harsh environments, ventilation and drainage facilities can be added to reduce the accumulation of corrosive media. At the same time, regular cleaning of the surface of H-beam and removal of attached corrosive substances are also effective preventive measures.
2. Strengthen maintenance and inspection
Regular inspection: Regularly inspect H-beams and observe the state of their surface coating or plating. Once the coating is found to be damaged or aged, it should be repaired or repainted in time to ensure the integrity of the protective layer.
Maintenance management: Strengthen the maintenance and management of H-beams, including regular cleaning, rust removal and repainting. At the same time, for parts that are difficult to paint, such as welds, bolted joints, etc., sacrificial anode protection or sealant filling can be used to enhance local corrosion resistance.
3. Other measures
Avoid the use of corrosive chemicals: During installation and use, chemicals that may cause corrosion, such as acidic cleaners, should be avoided. At the same time, for accessories such as fasteners, corrosion-resistant materials should also be selected to reduce corrosion sources.
Reasonable storage and transportation: When storing and transporting H-beams, care should be taken to avoid contact with corrosive substances, and try to maintain a dry and ventilated environment to reduce the risk of corrosion.