As an important building structural material, H-beam steel has been widely used in the construction field. However, the processing and cutting technology of H-beam steel has a vital impact on its application effect and life. This article will introduce the processing and cutting technology of H-beam steel in detail, in order to provide a reference for relevant practitioners.
Processing technology of H-beam steel:
H-beam steel is a kind of steel with excellent mechanical properties and processing properties. Its cross-sectional shape is similar to the English letter "H", hence the name. The processing technology of British standard H-shaped steel mainly includes the following steps:
1. Steel cutting: Cut the steel according to the required size, and flame cutting, laser cutting or plasma cutting can be used. Among them, laser cutting has the advantages of high cutting accuracy and good incision quality, but the cost is relatively high.
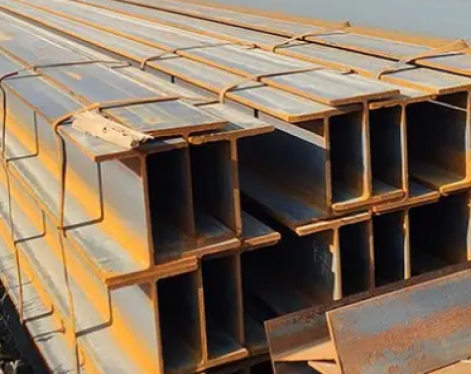
2. Steel straightening: Since steel will bend and twist during the rolling process, it needs to be straightened. Generally, mechanical straightening or hydraulic straightening is used to make the steel reach the required straightness.
3. Steel forming: According to the design requirements, the steel is bent and folded to form the required shape and size. During the forming process, care should be taken to avoid cracks or deformation of the steel.
4. Steel assembly: The formed steel is assembled according to the design requirements, which can be welded or bolted. During the assembly process, attention should be paid to ensuring the accuracy and positioning accuracy of each component.
5. Steel welding: For the parts that need to be welded, reasonable welding methods and process parameters are used for welding. During the welding process, attention should be paid to ensuring the quality of the weld and the smooth appearance.
6. Steel inspection: Inspect the processed H-shaped steel to check whether its size, shape, accuracy, etc. meet the design requirements. If there is any discrepancy, adjustment and correction are required.
H-beam steel cutting process:
The H-beam steel cutting process mainly involves flame cutting, laser cutting and plasma cutting. The following is a brief introduction and characteristics of these cutting methods:
1. Flame cutting
Flame cutting is a traditional cutting process that uses a high-temperature flame to partially melt the steel plate and quickly cool it to form a cutting surface. Flame cutting is mainly suitable for thicker steel plates, and has a faster cutting speed and lower cost. However, the accuracy of flame cutting is low, the surface roughness is large, and subsequent processing is required. At the same time, flame cutting will also produce smoke and harmful gases, which require environmental protection treatment.
2. Laser cutting
Laser cutting is a high-precision and high-efficiency cutting process. It irradiates a high-energy laser beam on the steel plate to partially melt the steel plate and quickly cool it to form a cutting surface. Laser cutting has high accuracy and low surface roughness, and is suitable for steel plates of various thicknesses. At the same time, laser cutting has high speed, high efficiency, and produces fewer pollutants. However, the cost of laser cutting is high, which may not be suitable for some small enterprises.
3. Plasma cutting
Plasma cutting is a cutting process between flame cutting and laser cutting. It uses a high-temperature plasma arc to partially melt the steel plate and quickly cool it to form a cutting surface. Plasma cutting has high accuracy, low surface roughness, high speed, and low cost. However, the pollution of plasma cutting is greater than that of flame cutting, and environmental protection treatment is required.
In summary, the cutting process of H-beam needs to be selected according to actual needs. If you need to cut thick steel plates quickly and at low cost, you can choose flame cutting; if you need to cut steel plates of various thicknesses with high precision and high efficiency, you can choose laser cutting; if you need to cut thick steel plates with high precision and low cost, you can choose plasma cutting. At the same time, for some large enterprises, these cutting methods can be combined according to actual conditions to achieve better processing effects and economic benefits.
Read more: Differences in the Process of Angle Steel and H-beam Steel
Processing technology of H-beam steel:
H-beam steel is a kind of steel with excellent mechanical properties and processing properties. Its cross-sectional shape is similar to the English letter "H", hence the name. The processing technology of British standard H-shaped steel mainly includes the following steps:
1. Steel cutting: Cut the steel according to the required size, and flame cutting, laser cutting or plasma cutting can be used. Among them, laser cutting has the advantages of high cutting accuracy and good incision quality, but the cost is relatively high.
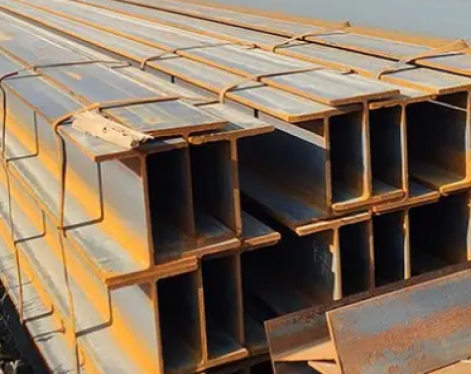
2. Steel straightening: Since steel will bend and twist during the rolling process, it needs to be straightened. Generally, mechanical straightening or hydraulic straightening is used to make the steel reach the required straightness.
3. Steel forming: According to the design requirements, the steel is bent and folded to form the required shape and size. During the forming process, care should be taken to avoid cracks or deformation of the steel.
4. Steel assembly: The formed steel is assembled according to the design requirements, which can be welded or bolted. During the assembly process, attention should be paid to ensuring the accuracy and positioning accuracy of each component.
5. Steel welding: For the parts that need to be welded, reasonable welding methods and process parameters are used for welding. During the welding process, attention should be paid to ensuring the quality of the weld and the smooth appearance.
6. Steel inspection: Inspect the processed H-shaped steel to check whether its size, shape, accuracy, etc. meet the design requirements. If there is any discrepancy, adjustment and correction are required.
H-beam steel cutting process:
The H-beam steel cutting process mainly involves flame cutting, laser cutting and plasma cutting. The following is a brief introduction and characteristics of these cutting methods:
1. Flame cutting
Flame cutting is a traditional cutting process that uses a high-temperature flame to partially melt the steel plate and quickly cool it to form a cutting surface. Flame cutting is mainly suitable for thicker steel plates, and has a faster cutting speed and lower cost. However, the accuracy of flame cutting is low, the surface roughness is large, and subsequent processing is required. At the same time, flame cutting will also produce smoke and harmful gases, which require environmental protection treatment.
2. Laser cutting
Laser cutting is a high-precision and high-efficiency cutting process. It irradiates a high-energy laser beam on the steel plate to partially melt the steel plate and quickly cool it to form a cutting surface. Laser cutting has high accuracy and low surface roughness, and is suitable for steel plates of various thicknesses. At the same time, laser cutting has high speed, high efficiency, and produces fewer pollutants. However, the cost of laser cutting is high, which may not be suitable for some small enterprises.
3. Plasma cutting
Plasma cutting is a cutting process between flame cutting and laser cutting. It uses a high-temperature plasma arc to partially melt the steel plate and quickly cool it to form a cutting surface. Plasma cutting has high accuracy, low surface roughness, high speed, and low cost. However, the pollution of plasma cutting is greater than that of flame cutting, and environmental protection treatment is required.
In summary, the cutting process of H-beam needs to be selected according to actual needs. If you need to cut thick steel plates quickly and at low cost, you can choose flame cutting; if you need to cut steel plates of various thicknesses with high precision and high efficiency, you can choose laser cutting; if you need to cut thick steel plates with high precision and low cost, you can choose plasma cutting. At the same time, for some large enterprises, these cutting methods can be combined according to actual conditions to achieve better processing effects and economic benefits.
Read more: Differences in the Process of Angle Steel and H-beam Steel