Welding in welded pipe is a method to control the hardness of the weld
(1) During the welding process, if the interlayer temperature is too high, the grains will be elongated and t8/5 will be increased. It cannot be normalized during on-site welding, and the original strength and toughness of the steel pipe will be lost. Therefore, the interlayer temperature must be strictly controlled during the welding process to prevent grain elongation.
(2) The constant temperature time, heating width, insulation thickness and insulation width of heat treatment are the main factors affecting the toughness of the weld. Appropriately prolonging the constant temperature time, increasing the heating width, heat preservation width, and heat preservation thickness will help to increase the tempering degree of the martensite structure and improve the toughness of the weld.
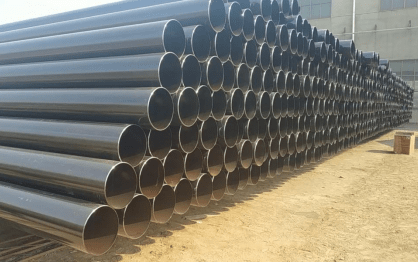
welding process
(1) Double-layer argon arc welding is adopted for the backing seam, and a 3.2mm electrode is used. The other layers adopt a multi-layer multi-pass welding process, and the thickness of a single layer is less than or equal to 3mm. During the welding process, the relationship between welding current and welding speed must be mastered. By reducing the thickness of the weld seam and the welding speed, a large-swing fast thin-layer welding operation technology is adopted.
(2) During welding, technicians measure the interlayer temperature of each layer of weld with a far-infrared temperature measuring gun, and the interlayer temperature is strictly controlled below 300 degrees (the interlayer temperature is 10~20mm in front of the molten pool, expressed as the highest value) . When the far-infrared temperature gun shows that the temperature exceeds 300 degrees, stop welding immediately, and continue welding when the temperature drops to 230 degrees.
After the welding of each layer is completed, technicians measure the thickness of the weld bead with a vernier caliper, and it is strictly forbidden to form a fillet weld between the weld bead and the groove, and the maximum thickness increase is less than or equal to 3 mm.
(1) During the welding process, if the interlayer temperature is too high, the grains will be elongated and t8/5 will be increased. It cannot be normalized during on-site welding, and the original strength and toughness of the steel pipe will be lost. Therefore, the interlayer temperature must be strictly controlled during the welding process to prevent grain elongation.
(2) The constant temperature time, heating width, insulation thickness and insulation width of heat treatment are the main factors affecting the toughness of the weld. Appropriately prolonging the constant temperature time, increasing the heating width, heat preservation width, and heat preservation thickness will help to increase the tempering degree of the martensite structure and improve the toughness of the weld.
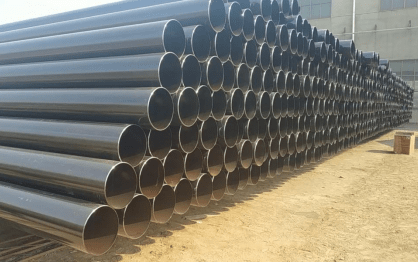
welding process
(1) Double-layer argon arc welding is adopted for the backing seam, and a 3.2mm electrode is used. The other layers adopt a multi-layer multi-pass welding process, and the thickness of a single layer is less than or equal to 3mm. During the welding process, the relationship between welding current and welding speed must be mastered. By reducing the thickness of the weld seam and the welding speed, a large-swing fast thin-layer welding operation technology is adopted.
(2) During welding, technicians measure the interlayer temperature of each layer of weld with a far-infrared temperature measuring gun, and the interlayer temperature is strictly controlled below 300 degrees (the interlayer temperature is 10~20mm in front of the molten pool, expressed as the highest value) . When the far-infrared temperature gun shows that the temperature exceeds 300 degrees, stop welding immediately, and continue welding when the temperature drops to 230 degrees.
After the welding of each layer is completed, technicians measure the thickness of the weld bead with a vernier caliper, and it is strictly forbidden to form a fillet weld between the weld bead and the groove, and the maximum thickness increase is less than or equal to 3 mm.