Lamellar tearing usually occurs in the welding of thick-walled seamless pipes. The main reason is that the MnS inclusions in the seamless pipe develop into cracks and then tear under the tensile stress perpendicular to the plate surface, resulting in low plastic failure of the structure. Thin-walled seamless pipes generally do not suffer from lamellar tearing problems due to less tensile stress in the direction of plate thickness. However, if there is segregation of MS inclusions in the thin-walled seamless pipe, when the pipe is subjected to tensile stress in the thickness direction, lamellar tearing will also occur.
What are the factors that affect lamellar tear?
1. The quantity, type and distribution of non-metallic inclusions are the essential cause of lamellar tearing and the root of the difference in the anomaly and mechanical properties of seamless pipes.
2. Z-direction restraint stress: The welded structure of thick-walled seamless pipe bears different Z-direction restraint stress, residual stress and post-weld load, which is the mechanical condition that causes lamellar tearing.
3. The influence of hydrogen: Generally, near the heat-affected zone, layer tearing is induced by cold cracking, and hydrogen is an important influencing factor.
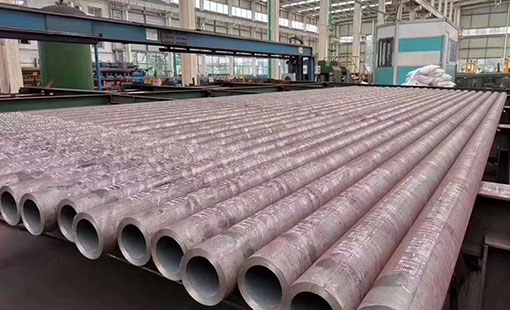
Due to the great impact and serious harm of delamination tearing, it is necessary to judge the sensitivity of seamless pipe layer tearing before construction. uation methods are:
For the Z-direction stretching section shrinkage method and the Z-direction critical stress method, the area shrinkage rate should not be less than 15%, and it is generally estimated that 15-20% is appropriate. For preventing lamellar tearing, when it is 25%, it is considered that the lamellar tearing resistance is excellent.
From the perspective of preventing delamination tearing, the construction technology and design are mainly to avoid stress concentration and Z-direction stress. The specific measures are as follows:
1. The use of double-sided welds can relieve the stress state in the root area of the weld, and single-sided welds should be avoided as much as possible to prevent stress concentration.
2. Use a symmetrical fillet weld with a small amount of welding instead of a full penetration weld with a large amount, which can effectively avoid excessive stress.
3. The groove is opened on the side bearing the Z-direction stress.
4. For T-shaped joints, a layer of low-strength welding material can be deposited on the transverse plate in advance to prevent cracks at the root of the weld and relieve welding strain.
5. Some measures to prevent cold cracking should be taken as much as possible to prevent layered tearing caused by cold cracking, such as appropriately increasing preheating, reducing hydrogen content, and controlling interlayer temperature.
What are the factors that affect lamellar tear?
1. The quantity, type and distribution of non-metallic inclusions are the essential cause of lamellar tearing and the root of the difference in the anomaly and mechanical properties of seamless pipes.
2. Z-direction restraint stress: The welded structure of thick-walled seamless pipe bears different Z-direction restraint stress, residual stress and post-weld load, which is the mechanical condition that causes lamellar tearing.
3. The influence of hydrogen: Generally, near the heat-affected zone, layer tearing is induced by cold cracking, and hydrogen is an important influencing factor.
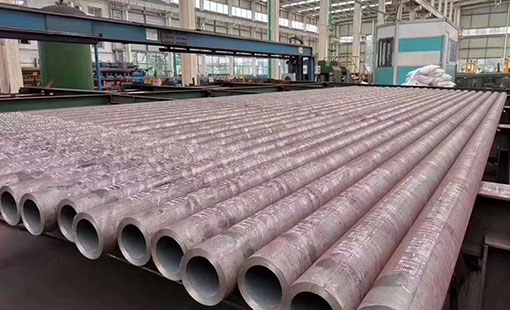
Due to the great impact and serious harm of delamination tearing, it is necessary to judge the sensitivity of seamless pipe layer tearing before construction. uation methods are:
For the Z-direction stretching section shrinkage method and the Z-direction critical stress method, the area shrinkage rate should not be less than 15%, and it is generally estimated that 15-20% is appropriate. For preventing lamellar tearing, when it is 25%, it is considered that the lamellar tearing resistance is excellent.
From the perspective of preventing delamination tearing, the construction technology and design are mainly to avoid stress concentration and Z-direction stress. The specific measures are as follows:
1. The use of double-sided welds can relieve the stress state in the root area of the weld, and single-sided welds should be avoided as much as possible to prevent stress concentration.
2. Use a symmetrical fillet weld with a small amount of welding instead of a full penetration weld with a large amount, which can effectively avoid excessive stress.
3. The groove is opened on the side bearing the Z-direction stress.
4. For T-shaped joints, a layer of low-strength welding material can be deposited on the transverse plate in advance to prevent cracks at the root of the weld and relieve welding strain.
5. Some measures to prevent cold cracking should be taken as much as possible to prevent layered tearing caused by cold cracking, such as appropriately increasing preheating, reducing hydrogen content, and controlling interlayer temperature.