H-beam rust hazards
From the appearance point of view, the surface of the rusted H-beam will be covered with mottled rust, and the originally smooth and flat surface will become rough, which greatly affects the overall aesthetics. In some construction projects with high requirements on appearance, rusted H-beam may directly damage the image of the project. From a performance perspective, rust has a fatal impact on the strength of H-beams. Rust is mainly composed of iron oxides, which are loose and fragile and cannot bear the same load as steel itself. As the degree of rust deepens, the effective cross-sectional area of the H-beam continues to decrease, just like a pillar gradually becomes thinner, and its load-bearing capacity will inevitably decrease.
Rust will also significantly shorten the service life of H-beams. Under normal circumstances, H-beams can be used stably for many years in a certain use environment, but once rusted, the corrosion rate will gradually accelerate. Without effective rust prevention treatment, H-beams that could have been used for decades may become unusable in just a few years due to severe rust, which undoubtedly increases replacement and maintenance costs.
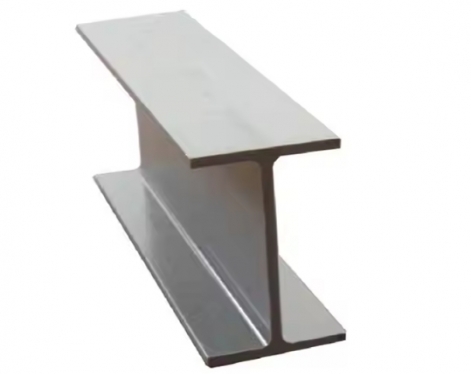
Reasons for H-beam rust
The rust of H-beam is the result of the combined effect of multiple factors. First of all, environmental factors are one of the important reasons for the rust of H-beam. When the humidity of the H-beam is high, the water vapor in the air will condense into a water film on its surface, and water is a necessary condition for the electrochemical corrosion of steel. In a humid environment, the iron on the surface of the H-beam reacts with water and oxygen to gradually generate rust.
Secondly, contact with corrosive substances is also a common cause of H-beam rust. If H-beam comes into direct contact with chemical substances such as acid, alkali, and salt, these substances will react chemically with the steel, destroying the passivation film on its surface and accelerating the rust process.
Long-term exposure to air is also a key factor in the rusting of H-beams. Even without a particularly harsh environment, the oxygen in the air will react with the iron on the surface of the H-beam to oxidize, and over time, rust will continue to accumulate.
In addition, damage to the surface protective layer of H-beam will also cause the steel to lose protection and come into direct contact with the external environment, thus causing rust. During transportation, installation or use, if the protective paint of the H-beam is scratched, worn, or the galvanized layer is damaged, it will not be able to effectively prevent the erosion of oxygen and moisture, thus causing rust.
How to prevent H-beam from rusting?
1. Surface treatment
Hot-dip galvanizing is a commonly used surface treatment method, in which H-beam is immersed in molten zinc liquid to form a zinc layer on its surface.
Spraying anti-rust paint is also a common method. Anti-rust paint works through the principles of physical rust prevention, chemical rust prevention and electrochemical rust prevention.
Electroplating is the process of depositing a metal coating on the surface of H-beam by electrolysis, such as zinc plating, nickel plating, etc. This method can make the coating uniform and dense, which can effectively improve the corrosion resistance and decorativeness of H-beam. It is often used for small H-beam products or parts with high requirements for appearance and corrosion resistance.
2. Environmental Control
When storing and using H-beam, environmental factors are crucial. The environment should be kept dry and ventilated, and the humidity should be controlled within an appropriate range to reduce the possibility of water vapor condensing into a water film on the surface of the H-beam. At the same time, H-beam should be kept away from corrosive substances such as acid, alkali, and salt to prevent chemical reactions from accelerating corrosion. In special environments such as chemical companies, special protective measures should be taken for h-beam to ensure that it does not come into contact with the surrounding corrosive media.
3. Regular maintenance
Regular maintenance is an important part of ensuring that H-beams do not rust for a long time. Check the surface condition of H-beams regularly to see if there are any rust spots and whether the protective layer is damaged. Once the protective layer is found to be scratched, worn or damaged, it should be repaired in time, re-sprayed with anti-rust paint or other protective treatments to prevent oxygen and moisture from corroding the steel through the damaged area. At the same time, regularly clean the dirt on the surface of the H-beam, because the dirt may contain corrosive substances, and long-term attachment to the surface will accelerate rust. Through regular maintenance, potential rust problems can be discovered and solved in time, extending the service life of the H-beam.
Read more: Advantages and Disadvantages of H-beam
From the appearance point of view, the surface of the rusted H-beam will be covered with mottled rust, and the originally smooth and flat surface will become rough, which greatly affects the overall aesthetics. In some construction projects with high requirements on appearance, rusted H-beam may directly damage the image of the project. From a performance perspective, rust has a fatal impact on the strength of H-beams. Rust is mainly composed of iron oxides, which are loose and fragile and cannot bear the same load as steel itself. As the degree of rust deepens, the effective cross-sectional area of the H-beam continues to decrease, just like a pillar gradually becomes thinner, and its load-bearing capacity will inevitably decrease.
Rust will also significantly shorten the service life of H-beams. Under normal circumstances, H-beams can be used stably for many years in a certain use environment, but once rusted, the corrosion rate will gradually accelerate. Without effective rust prevention treatment, H-beams that could have been used for decades may become unusable in just a few years due to severe rust, which undoubtedly increases replacement and maintenance costs.
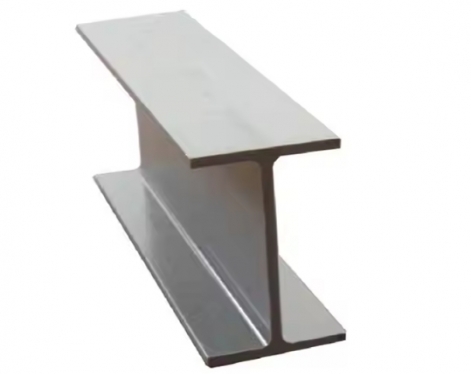
Reasons for H-beam rust
The rust of H-beam is the result of the combined effect of multiple factors. First of all, environmental factors are one of the important reasons for the rust of H-beam. When the humidity of the H-beam is high, the water vapor in the air will condense into a water film on its surface, and water is a necessary condition for the electrochemical corrosion of steel. In a humid environment, the iron on the surface of the H-beam reacts with water and oxygen to gradually generate rust.
Secondly, contact with corrosive substances is also a common cause of H-beam rust. If H-beam comes into direct contact with chemical substances such as acid, alkali, and salt, these substances will react chemically with the steel, destroying the passivation film on its surface and accelerating the rust process.
Long-term exposure to air is also a key factor in the rusting of H-beams. Even without a particularly harsh environment, the oxygen in the air will react with the iron on the surface of the H-beam to oxidize, and over time, rust will continue to accumulate.
In addition, damage to the surface protective layer of H-beam will also cause the steel to lose protection and come into direct contact with the external environment, thus causing rust. During transportation, installation or use, if the protective paint of the H-beam is scratched, worn, or the galvanized layer is damaged, it will not be able to effectively prevent the erosion of oxygen and moisture, thus causing rust.
How to prevent H-beam from rusting?
1. Surface treatment
Hot-dip galvanizing is a commonly used surface treatment method, in which H-beam is immersed in molten zinc liquid to form a zinc layer on its surface.
Spraying anti-rust paint is also a common method. Anti-rust paint works through the principles of physical rust prevention, chemical rust prevention and electrochemical rust prevention.
Electroplating is the process of depositing a metal coating on the surface of H-beam by electrolysis, such as zinc plating, nickel plating, etc. This method can make the coating uniform and dense, which can effectively improve the corrosion resistance and decorativeness of H-beam. It is often used for small H-beam products or parts with high requirements for appearance and corrosion resistance.
2. Environmental Control
When storing and using H-beam, environmental factors are crucial. The environment should be kept dry and ventilated, and the humidity should be controlled within an appropriate range to reduce the possibility of water vapor condensing into a water film on the surface of the H-beam. At the same time, H-beam should be kept away from corrosive substances such as acid, alkali, and salt to prevent chemical reactions from accelerating corrosion. In special environments such as chemical companies, special protective measures should be taken for h-beam to ensure that it does not come into contact with the surrounding corrosive media.
3. Regular maintenance
Regular maintenance is an important part of ensuring that H-beams do not rust for a long time. Check the surface condition of H-beams regularly to see if there are any rust spots and whether the protective layer is damaged. Once the protective layer is found to be scratched, worn or damaged, it should be repaired in time, re-sprayed with anti-rust paint or other protective treatments to prevent oxygen and moisture from corroding the steel through the damaged area. At the same time, regularly clean the dirt on the surface of the H-beam, because the dirt may contain corrosive substances, and long-term attachment to the surface will accelerate rust. Through regular maintenance, potential rust problems can be discovered and solved in time, extending the service life of the H-beam.
Read more: Advantages and Disadvantages of H-beam