In the modern industrial system, high-pressure boiler tubes play a pivotal role and are an indispensable component of many key equipment. They are mainly used to manufacture high-pressure and ultra-high-pressure steam boilers, with working pressures usually above 9.8MPa and working temperatures between 450℃ and 650℃, and are commonly found in the fields of electricity, chemical industry, petroleum, etc.
The performance of high-pressure boiler tubes is directly related to the safety and efficiency of the entire industrial system. As the core means to improve and optimize the performance of high-pressure boiler tubes, heat treatment technology has a key impact on them. Through appropriate heat treatment technology, the organizational structure of high-pressure boiler tubes can be significantly improved, making them have higher strength, better toughness, better high temperature resistance and corrosion resistance, thus meeting the stringent use requirements in industrial
production.
Characteristics of high pressure boiler tubes
1. Excellent high temperature and high pressure resistance:High-pressure boiler tubes are made of special alloy materials (such as pearlite heat-resistant steel) and undergo precision heat treatment technology. They can work stably for a long time in high-temperature and high-pressure environments up to 500°C, are not easy to deform or fail, and ensure efficient operation of the equipment.
2. Excellent corrosion resistance:The surface of the pipe forms a dense oxide film through alloy elements (such as chromium and molybdenum), which effectively resists corrosion from media such as steam and flue gas, prolongs the service life, and is especially suitable for high humidity and highly corrosive industrial environments.
3. High strength and high toughness:High-pressure boiler tubes have both high strength and good toughness. They can not only withstand pressure loads under high temperatures, but also have anti-fatigue properties, reducing the risk of cracks caused by long-term vibration or temperature fluctuations and ensuring equipment safety.
4. Precise processing adaptability:The pipes have undergone strict rolling and heat treatment, with high dimensional accuracy and smooth surface, which is convenient for welding, bending and other processing operations. They can be flexibly adapted to different boiler structure designs and reduce installation and maintenance costs.
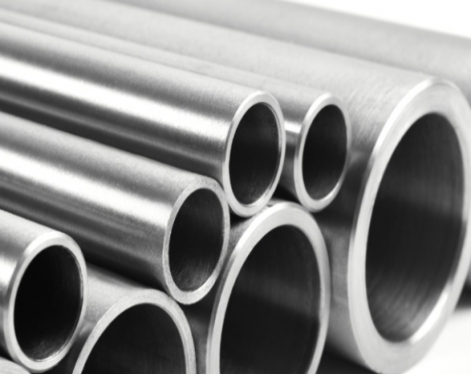
Heat treatment process secrets
1. Annealing: The Magic of Stress Relief
Annealing is a commonly used process in heat treatment of high-pressure boiler tubes. Its purpose is to eliminate the stress generated in the high-pressure boiler tubes during forging, rolling and welding, and improve their mechanical properties. After annealing, the internal stress of the high-pressure boiler tube is released, the hardness is reduced, the plasticity and toughness are improved, and it can better meet the requirements of subsequent processing and use, just like "loosening" the tired material and restoring it to a good state.
2. Normalizing: Improve hardness and strength
The main function of normalizing is to improve the hardness and strength of high-pressure boiler tubes so that they can better adapt to the high-pressure and high-temperature working environment. During the normalizing process, the high-pressure boiler tubes are heated above the critical temperature. For example, for 20G, 20MNG, and 25MNG steel grades, the normalizing temperature is 880℃ - 940℃. After keeping warm for a period of time, it is cooled naturally in the air. Rapid cooling makes the structure of the high-pressure boiler tube more compact, thereby improving its hardness and strength, allowing it to function stably under harsh working conditions.
3. Quenching: Hardening by rapid cooling
Quenching is a heat treatment method that rapidly cools high-pressure boiler tubes to obtain high hardness. First, heat the high-pressure boiler tube to above the critical temperature, keep it warm for a certain period of time, and then quickly put it into the quenching medium to cool it down. The quenching temperature is generally between 850℃ - 950℃, and the quenching media include water, oil, etc. For example, for some high-pressure boiler tubes that require higher hardness, water quenching will be chosen to obtain higher hardness. However, although the hardness of the high-pressure boiler tube after quenching is high, it is also very brittle, has high internal stress, and is prone to cracking, so it is usually properly annealed or normalized before quenching.
4. Tempering: Stress relief and toughness improvement
Tempering is carried out immediately after quenching, the purpose of which is to eliminate the internal stress generated by quenching, reduce brittleness, and improve the toughness and plasticity of high-pressure boiler tubes. During tempering, the quenched high-pressure boiler tube is reheated to a certain temperature, such as low-temperature tempering temperature at 150℃ - 250℃, medium-temperature tempering at 350℃ - 500℃, and high-temperature tempering at 500℃ - 650℃, and then cooled after keeping warm for a period of time. Tempering can reduce the hardness to a certain extent, but in return it greatly improves the toughness, making the comprehensive performance of the high-pressure boiler tube more balanced and adaptable to different working requirements.
Read more: High-pressure Boiler Tube Welding Steps
The performance of high-pressure boiler tubes is directly related to the safety and efficiency of the entire industrial system. As the core means to improve and optimize the performance of high-pressure boiler tubes, heat treatment technology has a key impact on them. Through appropriate heat treatment technology, the organizational structure of high-pressure boiler tubes can be significantly improved, making them have higher strength, better toughness, better high temperature resistance and corrosion resistance, thus meeting the stringent use requirements in industrial
production.
Characteristics of high pressure boiler tubes
1. Excellent high temperature and high pressure resistance:High-pressure boiler tubes are made of special alloy materials (such as pearlite heat-resistant steel) and undergo precision heat treatment technology. They can work stably for a long time in high-temperature and high-pressure environments up to 500°C, are not easy to deform or fail, and ensure efficient operation of the equipment.
2. Excellent corrosion resistance:The surface of the pipe forms a dense oxide film through alloy elements (such as chromium and molybdenum), which effectively resists corrosion from media such as steam and flue gas, prolongs the service life, and is especially suitable for high humidity and highly corrosive industrial environments.
3. High strength and high toughness:High-pressure boiler tubes have both high strength and good toughness. They can not only withstand pressure loads under high temperatures, but also have anti-fatigue properties, reducing the risk of cracks caused by long-term vibration or temperature fluctuations and ensuring equipment safety.
4. Precise processing adaptability:The pipes have undergone strict rolling and heat treatment, with high dimensional accuracy and smooth surface, which is convenient for welding, bending and other processing operations. They can be flexibly adapted to different boiler structure designs and reduce installation and maintenance costs.
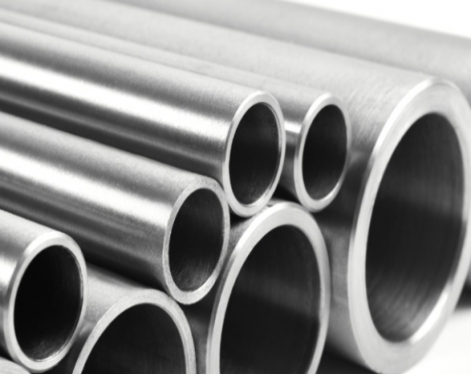
Heat treatment process secrets
1. Annealing: The Magic of Stress Relief
Annealing is a commonly used process in heat treatment of high-pressure boiler tubes. Its purpose is to eliminate the stress generated in the high-pressure boiler tubes during forging, rolling and welding, and improve their mechanical properties. After annealing, the internal stress of the high-pressure boiler tube is released, the hardness is reduced, the plasticity and toughness are improved, and it can better meet the requirements of subsequent processing and use, just like "loosening" the tired material and restoring it to a good state.
2. Normalizing: Improve hardness and strength
The main function of normalizing is to improve the hardness and strength of high-pressure boiler tubes so that they can better adapt to the high-pressure and high-temperature working environment. During the normalizing process, the high-pressure boiler tubes are heated above the critical temperature. For example, for 20G, 20MNG, and 25MNG steel grades, the normalizing temperature is 880℃ - 940℃. After keeping warm for a period of time, it is cooled naturally in the air. Rapid cooling makes the structure of the high-pressure boiler tube more compact, thereby improving its hardness and strength, allowing it to function stably under harsh working conditions.
3. Quenching: Hardening by rapid cooling
Quenching is a heat treatment method that rapidly cools high-pressure boiler tubes to obtain high hardness. First, heat the high-pressure boiler tube to above the critical temperature, keep it warm for a certain period of time, and then quickly put it into the quenching medium to cool it down. The quenching temperature is generally between 850℃ - 950℃, and the quenching media include water, oil, etc. For example, for some high-pressure boiler tubes that require higher hardness, water quenching will be chosen to obtain higher hardness. However, although the hardness of the high-pressure boiler tube after quenching is high, it is also very brittle, has high internal stress, and is prone to cracking, so it is usually properly annealed or normalized before quenching.
4. Tempering: Stress relief and toughness improvement
Tempering is carried out immediately after quenching, the purpose of which is to eliminate the internal stress generated by quenching, reduce brittleness, and improve the toughness and plasticity of high-pressure boiler tubes. During tempering, the quenched high-pressure boiler tube is reheated to a certain temperature, such as low-temperature tempering temperature at 150℃ - 250℃, medium-temperature tempering at 350℃ - 500℃, and high-temperature tempering at 500℃ - 650℃, and then cooled after keeping warm for a period of time. Tempering can reduce the hardness to a certain extent, but in return it greatly improves the toughness, making the comprehensive performance of the high-pressure boiler tube more balanced and adaptable to different working requirements.
Read more: High-pressure Boiler Tube Welding Steps