The offset defect of ERW pipe, also called lap welding, refers to the misalignment of the two edges of the tube blank during welding. Even after the internal and external burrs are removed, traces of offset can still be seen on the inner and outer surfaces of the steel pipe.
The main hazard of offset is to reduce the effective wall thickness of the steel pipe. The API SPEC 5L standard stipulates that the offset plus residual burrs of electric welded steel pipes shall not exceed 1.5mm (0.060 in). In addition, offset will also affect the ultrasonic and X-ray inspection of steel pipes. During the use of the steel pipe, the offset will also become the starting point of the chemical corrosion of the steel pipe.
Causes of offset defects in ERW steel pipes
1. Offset caused by poor molding quality
ERW steel pipe needs to go through a series of rolls (coarse forming roll string, fine forming) to gradually roll the coil into a barrel shape, and the forming quality has a great influence on the welding quality. If the center of the steel strip is shifted during forming, it will cause the edge of the tube blank to be uneven and produce an offset. Usually, this offset is in one direction, which is easier to judge. Secondly, if the parameters of the forming roll are not set properly, before entering the extrusion roll, the height of the two edges of the strip changes in a wave shape, and after entering the extrusion roll, a local small offset occurs, and the direction of the offset is uncertain.
2. The influence of extrusion force
The ERW steel pipe is welded by heating the edge of the strip and extruded by the extrusion roller. The extrusion force is one of the main parameters of the welding process and has a great influence on the quality of the ERW steel pipe. The extrusion force is small, the number of eutectics formed is small, and the weld strength is low. At the same time, non-metallic inclusions and oxide residues formed in the weld also affect the weld strength. If the extrusion force is too large, all the metal that reaches the welding temperature will be squeezed out, which will reduce the strength of the weld. In addition, excessive extrusion force is easy to form an offset, and it is difficult to adjust this offset without reducing the extrusion force. In general, the extrusion force is expressed and calculated by the circumference difference of the tube billet before and after the extrusion roller - the extrusion amount, which is usually half of the wall thickness of the steel pipe.
3. The impact of rolls and tooling
(1) The influence of the roll. The rolls that affect the offset of ERW steel pipes are mainly fine-formed rolls and squeeze rolls. The wear of the fine-formed rolls is too large, and the wear on both sides of the guide pieces of the fine-formed rolls is different. The edge damage of the squeeze roller, especially the upper squeeze roller, and the difference in the wear of the two squeeze rollers will cause offset, which generally has a certain period.
(2) The influence of the roll bearing. The bearing damage of the extrusion roller causes the extrusion roller to not rotate or rotate unevenly, resulting in uneven extrusion force, and offset will occur. In addition, a large amount of bearing wear or a large bearing clearance will also cause uneven rotation of the squeeze roller, resulting in offset
(3) The influence of the installation quality of the roll tooling. The finishing roll and the side extrusion roll are not installed horizontally, and the gap between the upper extrusion roll shaft and bearing and the gap between the shaft and the roll seat is too large, which will cause offset
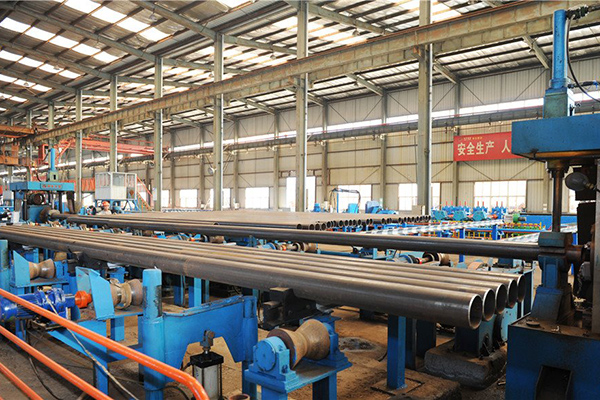
Judgment and confirmation of offset
The judgment and confirmation of offset mainly depends on visual observation. When there is an obvious offset, it can be found after squeezing the roller. However, for small offsets, it is necessary to observe the internal and external burrs and the shape of the weld seam after the internal and external burrs are removed. It can be judged from the following aspects.
(1) Observe the outer burr, the melt extruded by welding is not in the middle of the outer burr.
(2) The outer weld bead is not straight after the burr is removed, and the width and shape of the outer weld bead after scraping change.
(3) Observe the inner burr, if the inner burr has intermittent splits or cracks, there may be an offset defect
Adjustment and elimination of offset
When an offset occurs, judge the cause of the offset according to the offset phenomenon, and take the following measures to adjust:
(1) After the strip enters the forming machine, make sure that the center of the strip does not deviate from the rolling center. When there are waves and bulges on the edge of the tube blank, reasonably adjust the fine forming diameter reduction and the reduction of the small row of rollers to reduce and eliminate the edge waves and bulges.
(2) Select reasonable process parameters, especially suitable welding extrusion force.
(3) Grind the rolls with excessive wear or different wear on both sides of the finely formed roll guide, and repair the squeeze rolls with edge damage
(4) Check and replace bearings with large wear or large bearing clearance, and do a good job of lubricating the bearings.
(5) Ensure that the rolls are installed horizontally when changing lanes, and eliminate the excessive gap between the extrusion shaft and the bearing, and the shaft and the roll seat.
ERW pipe is a welded steel tube supported by the electric resistance welding process. Resistance welding is a method of combining the workpieces and applying pressure through the electrodes, using the resistance heat generated by the current passing through the contact surface of the joint and the adjacent area for welding. Resistance welding is a method in which the current flows through the contact surface of the workpiece and the adjacent area to heat it to a molten or plastic state to form a metal bond.
The main hazard of offset is to reduce the effective wall thickness of the steel pipe. The API SPEC 5L standard stipulates that the offset plus residual burrs of electric welded steel pipes shall not exceed 1.5mm (0.060 in). In addition, offset will also affect the ultrasonic and X-ray inspection of steel pipes. During the use of the steel pipe, the offset will also become the starting point of the chemical corrosion of the steel pipe.
Causes of offset defects in ERW steel pipes
1. Offset caused by poor molding quality
ERW steel pipe needs to go through a series of rolls (coarse forming roll string, fine forming) to gradually roll the coil into a barrel shape, and the forming quality has a great influence on the welding quality. If the center of the steel strip is shifted during forming, it will cause the edge of the tube blank to be uneven and produce an offset. Usually, this offset is in one direction, which is easier to judge. Secondly, if the parameters of the forming roll are not set properly, before entering the extrusion roll, the height of the two edges of the strip changes in a wave shape, and after entering the extrusion roll, a local small offset occurs, and the direction of the offset is uncertain.
2. The influence of extrusion force
The ERW steel pipe is welded by heating the edge of the strip and extruded by the extrusion roller. The extrusion force is one of the main parameters of the welding process and has a great influence on the quality of the ERW steel pipe. The extrusion force is small, the number of eutectics formed is small, and the weld strength is low. At the same time, non-metallic inclusions and oxide residues formed in the weld also affect the weld strength. If the extrusion force is too large, all the metal that reaches the welding temperature will be squeezed out, which will reduce the strength of the weld. In addition, excessive extrusion force is easy to form an offset, and it is difficult to adjust this offset without reducing the extrusion force. In general, the extrusion force is expressed and calculated by the circumference difference of the tube billet before and after the extrusion roller - the extrusion amount, which is usually half of the wall thickness of the steel pipe.
3. The impact of rolls and tooling
(1) The influence of the roll. The rolls that affect the offset of ERW steel pipes are mainly fine-formed rolls and squeeze rolls. The wear of the fine-formed rolls is too large, and the wear on both sides of the guide pieces of the fine-formed rolls is different. The edge damage of the squeeze roller, especially the upper squeeze roller, and the difference in the wear of the two squeeze rollers will cause offset, which generally has a certain period.
(2) The influence of the roll bearing. The bearing damage of the extrusion roller causes the extrusion roller to not rotate or rotate unevenly, resulting in uneven extrusion force, and offset will occur. In addition, a large amount of bearing wear or a large bearing clearance will also cause uneven rotation of the squeeze roller, resulting in offset
(3) The influence of the installation quality of the roll tooling. The finishing roll and the side extrusion roll are not installed horizontally, and the gap between the upper extrusion roll shaft and bearing and the gap between the shaft and the roll seat is too large, which will cause offset
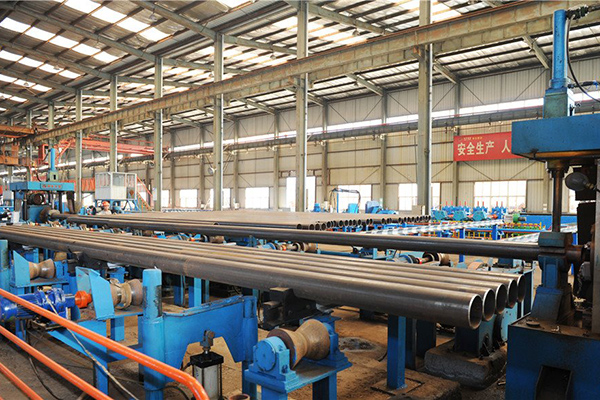
Judgment and confirmation of offset
The judgment and confirmation of offset mainly depends on visual observation. When there is an obvious offset, it can be found after squeezing the roller. However, for small offsets, it is necessary to observe the internal and external burrs and the shape of the weld seam after the internal and external burrs are removed. It can be judged from the following aspects.
(1) Observe the outer burr, the melt extruded by welding is not in the middle of the outer burr.
(2) The outer weld bead is not straight after the burr is removed, and the width and shape of the outer weld bead after scraping change.
(3) Observe the inner burr, if the inner burr has intermittent splits or cracks, there may be an offset defect
Adjustment and elimination of offset
When an offset occurs, judge the cause of the offset according to the offset phenomenon, and take the following measures to adjust:
(1) After the strip enters the forming machine, make sure that the center of the strip does not deviate from the rolling center. When there are waves and bulges on the edge of the tube blank, reasonably adjust the fine forming diameter reduction and the reduction of the small row of rollers to reduce and eliminate the edge waves and bulges.
(2) Select reasonable process parameters, especially suitable welding extrusion force.
(3) Grind the rolls with excessive wear or different wear on both sides of the finely formed roll guide, and repair the squeeze rolls with edge damage
(4) Check and replace bearings with large wear or large bearing clearance, and do a good job of lubricating the bearings.
(5) Ensure that the rolls are installed horizontally when changing lanes, and eliminate the excessive gap between the extrusion shaft and the bearing, and the shaft and the roll seat.
ERW pipe is a welded steel tube supported by the electric resistance welding process. Resistance welding is a method of combining the workpieces and applying pressure through the electrodes, using the resistance heat generated by the current passing through the contact surface of the joint and the adjacent area for welding. Resistance welding is a method in which the current flows through the contact surface of the workpiece and the adjacent area to heat it to a molten or plastic state to form a metal bond.
Previous:ERW pipe mill line