Thermally expanded seamless pipe is what we often call thermally expanded pipe. Steel pipes with relatively low density but strong shrinkage (seamless steel pipe) can be referred to as thermally expanded pipes. A rough tube finish rolling process that expands the diameter of the tube by cross rolling or drawing. In a short period of time, the steel pipe can be thickened to produce non-standard and special-type seamless pipes with low cost and high production efficiency, which is the current development trend in the international pipe rolling field.
The warp expansion of heat-expanded seamless steel pipe is a pressure processing process that applies force from the inner wall of the steel pipe by hydraulic or mechanical means to expand the steel pipe radially outward. The mechanical method is simpler and more efficient than the hydraulic method. The process is:
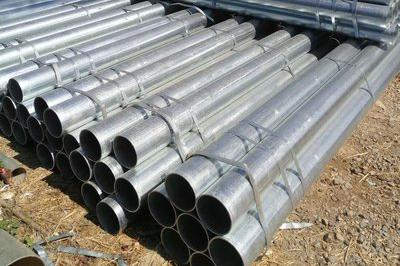
Mechanical expansion utilizes the segmental block at the end of the expansion machine to expand in the radial direction, so that the tube blank can be plastically deformed in steps along the length direction, and the process of plastic deformation of the entire tube length is realized in sections, thereby producing heat-expanded seamless steel tubes. There are 5 stages:
1. Preliminary full circle stage. The fan-shaped blocks are opened until all the fan-shaped blocks touch the inner wall of the steel pipe. At this time, the radii of all points in the inner circular pipe of the steel pipe within the step range are almost the same, and the steel pipe obtains a preliminary full circle.
2. Nominal inner diameter stage. The fan-shaped block starts to reduce the moving speed from the front position until it reaches the required position, which is the inner circumference position of the finished tube required by the quality.
3. Springback compensation stage. The fan-shaped block starts to lower the speed at the position of the second stage until it reaches the required position, which is the position of the inner circumference of the steel pipe before springback required by the process design.
4. Stable pressure holding stage. The fan-shaped block remains stationary for a period of time at the inner circumference of the steel pipe before springing back, which is the pressure-holding and stable stage required by the equipment and diameter-expanding process.
5. Unloading regression stage. The fan-shaped block retracts rapidly from the inner circumference of the steel pipe before springing back, until it reaches the initial diameter expansion position, which is the minimum shrinkage diameter of the fan-shaped block required by the diameter expansion process.
In practical application, in process simplification, steps 2 and 3 can be combined and simplified, which has no effect on the diameter expansion quality of steel pipes.
The warp expansion of heat-expanded seamless steel pipe is a pressure processing process that applies force from the inner wall of the steel pipe by hydraulic or mechanical means to expand the steel pipe radially outward. The mechanical method is simpler and more efficient than the hydraulic method. The process is:
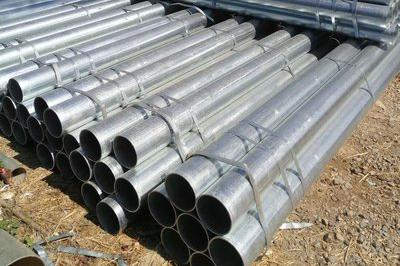
Mechanical expansion utilizes the segmental block at the end of the expansion machine to expand in the radial direction, so that the tube blank can be plastically deformed in steps along the length direction, and the process of plastic deformation of the entire tube length is realized in sections, thereby producing heat-expanded seamless steel tubes. There are 5 stages:
1. Preliminary full circle stage. The fan-shaped blocks are opened until all the fan-shaped blocks touch the inner wall of the steel pipe. At this time, the radii of all points in the inner circular pipe of the steel pipe within the step range are almost the same, and the steel pipe obtains a preliminary full circle.
2. Nominal inner diameter stage. The fan-shaped block starts to reduce the moving speed from the front position until it reaches the required position, which is the inner circumference position of the finished tube required by the quality.
3. Springback compensation stage. The fan-shaped block starts to lower the speed at the position of the second stage until it reaches the required position, which is the position of the inner circumference of the steel pipe before springback required by the process design.
4. Stable pressure holding stage. The fan-shaped block remains stationary for a period of time at the inner circumference of the steel pipe before springing back, which is the pressure-holding and stable stage required by the equipment and diameter-expanding process.
5. Unloading regression stage. The fan-shaped block retracts rapidly from the inner circumference of the steel pipe before springing back, until it reaches the initial diameter expansion position, which is the minimum shrinkage diameter of the fan-shaped block required by the diameter expansion process.
In practical application, in process simplification, steps 2 and 3 can be combined and simplified, which has no effect on the diameter expansion quality of steel pipes.