(1)Material Selection
The raw material for stainless steel plates consists of iron alloys containing added elements such as chromium, nickel, silicon, manganese, nitrogen, and carbon. The performance of the final alloy can be finely adjusted by changing the amounts of these alloying elements. Among them, chromium is the most important element in the manufacture of stainless steel, which is essential for the production of stainless steel and currently has no viable alternative methods. Chromium is a hard, corrosion-resistant transition element that can provide corrosion resistance to stainless steel plates. Generally speaking, the higher the chromium content, the more corrosion-resistant the stainless steel.
(2)Melting
After the raw materials are selected, the production and manufacturing process of stainless steel begins with melting, which is the fusion of the raw materials together in an electric arc furnace.(3)Removal of Impurities
Next is the removal of excess carbon elements, which is accomplished by processing the molten metal in an AOD (Argon Oxygen Decarburization) converter. The AOD converter reduces carbon by injecting a mixture of oxygen and argon. At this stage, other alloying elements such as nickel and molybdenum can be added to the AOD converter. When a very low carbon content is required, a VOD (Vacuum Oxygen Decarburization) converter can be used.
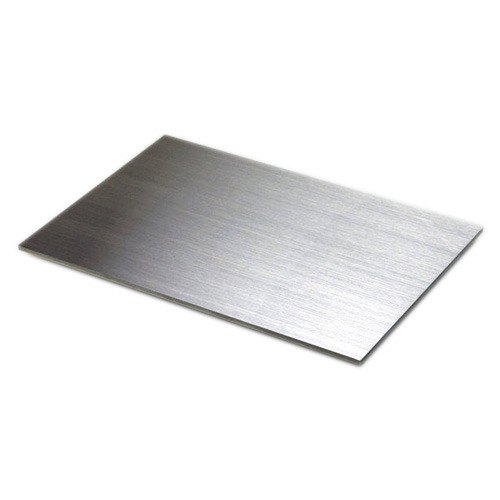
(4)Chemical Composition Adjustment
Following this is the adjustment phase, where most stainless steels have very strict quality requirements. The adjustment process even allows for fine-tuning of the chemical composition. Adjustment involves slowly stirring the steel to remove unwanted elements and increase viscosity while maintaining the required composition within temperature limits.
(5)Casting
The casting step involves pouring the molten steel into shapes. These forms can be patterned (rectangular), billets (round or square), plates, bars, or tubes.
(6)Hot Rolling
Then comes hot rolling, which occurs at temperatures above the steel's recrystallization temperature. The exact temperature depends on the grade of stainless steel required. The stainless steel plates are heated and passed through tall rolls. Billets and blooms form bars and wires, while slabs form plates, strips, and sheets.
(7)Cold Rolling (if necessary)
If necessary, cold rolling can also be performed, which is commonly used for stainless steel plates that require very precise dimensions or attractive surface finishes. This process takes place below the steel's recrystallization temperature, using small-diameter rolls and a series of support rolls. This process allows for the production of wide sheets with improved surface finish.(8)Annealing
After rolling, the stainless steel plates undergo an annealing treatment, which is a process used to soften the stainless steel, improve ductility, and refine the grain structure. It is also used to relieve internal stresses caused by previous processing. During annealing, the steel is heated and cooled under controlled conditions.(9)Descalving
After annealing, it is necessary to descale because the annealing process can cause scale to form on the steel. These scales are typically removed by pickling, which involves immersing the stainless steel plates in a mixture of nitric acid and hydrofluoric acid. Electrocleaning is another method that uses an electric current to remove the oxide scale.
(10)Cutting
Then comes the cutting process, where the stainless steel plates can now be cut to the required sizes. Mechanical cutting is the most common method. Stainless steel plates can be cut straight with shearing knives, cut into circles with circular knives, cut with high-speed blades, or punched with punches and dies. Other methods include flame cutting, which uses a cutting torch powered by oxygen, propane, and iron powder, or plasma cutting, which uses an ionized gas column with an electric arc to cut the metal.
(11)Finishing
Finally, there is finishing, as surface finish is very important for stainless steel plate products, especially in applications where appearance is important. Grinding wheels or sand belts are commonly used for grinding or polishing the steel. Other methods include polishing with cloth wheels containing abrasive particles, dry etching with sandblasting, and wet etching with acid solutions. In addition, the smooth surface of the stainless steel plate also provides better corrosion resistance.Through the above steps, stainless steel sheets with good corrosion resistance and an attractive appearance can be produced to meet the needs of various applications.