(1)Mirror Finish
This involves polishing the stainless steel plate surface to a mirror-like shine. Further treatments like titanium plating and etching can be done afterward. The professional term for this is 8K, with grades including 6K, 8K, Super 8K, and Ultra Super 8K. The difference lies in the level of brightness and control of surface defects.
For different thicknesses:
Machine grinding for 8K is available for thicknesses 0.3-3.0mm and lengths over 1.6m to 4.5m.
Manual grinding for 8K is required for plates over 3.0mm thick, with lengths as needed.
The 8K grinding process includes: trimming, machine entry, coarse grinding, fine grinding, cleaning, drying, and film application.
Quality inspection standards: The surface must not have insufficient brightness, surface defects, creases, damage, or residual stains. The film application must be even.
(2)Brushed Finish (also known as Satin or Hairline)
This process uses a high-speed sanding belt to grind the stainless steel sheet surface, creating regular patterns. There are various types of sanding, such as ordinary sand, snowflake sand, straight lines, combinations, etc. The finer the sandpaper, the finer the texture, and vice versa.
The brushed process includes: changing the sanding belt, trimming, oiling, brushing, degreasing, cleaning, drying, and film application.
Quality inspection standards: The surface texture should be even, without fingerprints, scratches, marks, or uneven film application.
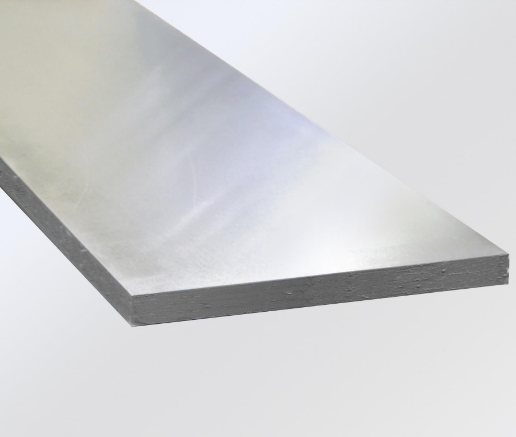
(3)Etching
This process uses a mold to print patterns on the stainless steel surface with ink, then chemically etches the uncoated areas to reveal the pattern.
There are three types of etching:
Photo-etching for irregular sizes, small batches, or parts, with depths over 20C.
Screen printing etching for fixed sizes and large batches, with depths up to 15C.
Titanium etching for surface color oxidation without depth.
The etching process includes: printing (inking), exposure, machine entry, etching, ink removal, cleaning, drying, and film application.
Quality inspection standards: The surface should be free of acid spots, rough edges, and ink.
(4)Vacuum Coating
This process involves ionizing target materials in a vacuum furnace and injecting gases (oxygen, nitrogen, acetylene) to form a metal color film on the stainless steel surface. It enhances corrosion resistance, hardness, wear prevention, conductivity, lubricity, heat resistance, and appearance.
Available colors include titanium gold, rose gold, copper, black titanium, sapphire blue, emerald green, pink, champagne gold, coffee gold, and violet.
The coating process includes: trimming, drilling, washing, loading, vacuum furnace, unloading, film application, and quality inspection.
Quality inspection standards: The color should be uniform without fingerprints, sweat marks, or scratches.
(5)Water Black Titanium
This process involves placing the stainless steel in a chemical bath to achieve a blackened effect. The color is deeper than vacuum coating, with 90% color difference controllability.
The water black titanium process includes: trimming, drilling, washing, chemical bath, cleaning, drying, and film application.
(6)Water Copper Plating
This process involves placing the panel in a chemical bath to plate copper powder on the stainless steel surface, achieving an antique copper effect.The water copper process includes: sanding, high-temperature degreasing, nickel plating (for better copper adhesion), copper plating, blackening, cleaning, drying, finishing, oiling, and film application.
(7)Sandblasting
This process uses compressed air to propel abrasive particles onto the workpiece surface, creating a textured effect.
The sandblasting process includes: changing the grit, machine entry, cleaning, blasting, removing loose sand, and film application.
(8)Random Pattern
This process uses a high-speed sanding belt to create circular patterns on the stainless steel surface.
(9)Lamination and Heat Transfer (Wood Grain):
This process involves adhering a film to the stainless steel surface with glue and high temperature, or transferring a printed pattern onto the surface. Lamination and heat transfer can be done on various surfaces and patterns, but they differ in use; laminated panels may delaminate when bent, while heat transfer panels generally do not.
(10)Laser Etching
This process uses a machine to grind the stainless steel surface to create a pattern without a tactile feel, such as CD shapes or other designs.
(11)Fingerprint-Resistant (Anti-Fingerprint)
This is the final process for all treatments, applying a transparent nano-oil on the surface to create a protective layer. It is not suitable for high-temperature environments.
(12)Embossing
This process uses an engraved roller to press patterns into stainless steel coils, creating a textured surface similar to etching but with smoother edges.
This involves polishing the stainless steel plate surface to a mirror-like shine. Further treatments like titanium plating and etching can be done afterward. The professional term for this is 8K, with grades including 6K, 8K, Super 8K, and Ultra Super 8K. The difference lies in the level of brightness and control of surface defects.
For different thicknesses:
Machine grinding for 8K is available for thicknesses 0.3-3.0mm and lengths over 1.6m to 4.5m.
Manual grinding for 8K is required for plates over 3.0mm thick, with lengths as needed.
The 8K grinding process includes: trimming, machine entry, coarse grinding, fine grinding, cleaning, drying, and film application.
Quality inspection standards: The surface must not have insufficient brightness, surface defects, creases, damage, or residual stains. The film application must be even.
(2)Brushed Finish (also known as Satin or Hairline)
This process uses a high-speed sanding belt to grind the stainless steel sheet surface, creating regular patterns. There are various types of sanding, such as ordinary sand, snowflake sand, straight lines, combinations, etc. The finer the sandpaper, the finer the texture, and vice versa.
The brushed process includes: changing the sanding belt, trimming, oiling, brushing, degreasing, cleaning, drying, and film application.
Quality inspection standards: The surface texture should be even, without fingerprints, scratches, marks, or uneven film application.
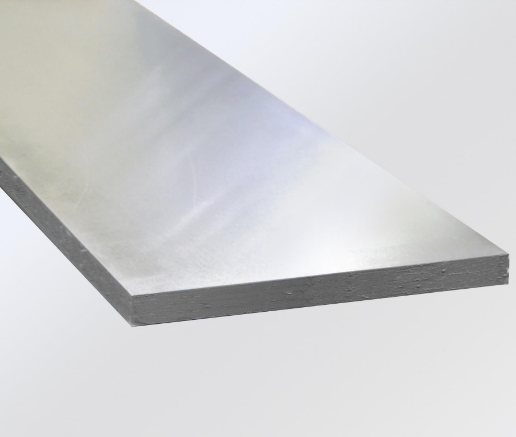
(3)Etching
This process uses a mold to print patterns on the stainless steel surface with ink, then chemically etches the uncoated areas to reveal the pattern.
There are three types of etching:
Photo-etching for irregular sizes, small batches, or parts, with depths over 20C.
Screen printing etching for fixed sizes and large batches, with depths up to 15C.
Titanium etching for surface color oxidation without depth.
The etching process includes: printing (inking), exposure, machine entry, etching, ink removal, cleaning, drying, and film application.
Quality inspection standards: The surface should be free of acid spots, rough edges, and ink.
(4)Vacuum Coating
This process involves ionizing target materials in a vacuum furnace and injecting gases (oxygen, nitrogen, acetylene) to form a metal color film on the stainless steel surface. It enhances corrosion resistance, hardness, wear prevention, conductivity, lubricity, heat resistance, and appearance.
Available colors include titanium gold, rose gold, copper, black titanium, sapphire blue, emerald green, pink, champagne gold, coffee gold, and violet.
The coating process includes: trimming, drilling, washing, loading, vacuum furnace, unloading, film application, and quality inspection.
Quality inspection standards: The color should be uniform without fingerprints, sweat marks, or scratches.
(5)Water Black Titanium
This process involves placing the stainless steel in a chemical bath to achieve a blackened effect. The color is deeper than vacuum coating, with 90% color difference controllability.
The water black titanium process includes: trimming, drilling, washing, chemical bath, cleaning, drying, and film application.
(6)Water Copper Plating
This process involves placing the panel in a chemical bath to plate copper powder on the stainless steel surface, achieving an antique copper effect.The water copper process includes: sanding, high-temperature degreasing, nickel plating (for better copper adhesion), copper plating, blackening, cleaning, drying, finishing, oiling, and film application.
(7)Sandblasting
This process uses compressed air to propel abrasive particles onto the workpiece surface, creating a textured effect.
The sandblasting process includes: changing the grit, machine entry, cleaning, blasting, removing loose sand, and film application.
(8)Random Pattern
This process uses a high-speed sanding belt to create circular patterns on the stainless steel surface.
(9)Lamination and Heat Transfer (Wood Grain):
This process involves adhering a film to the stainless steel surface with glue and high temperature, or transferring a printed pattern onto the surface. Lamination and heat transfer can be done on various surfaces and patterns, but they differ in use; laminated panels may delaminate when bent, while heat transfer panels generally do not.
(10)Laser Etching
This process uses a machine to grind the stainless steel surface to create a pattern without a tactile feel, such as CD shapes or other designs.
(11)Fingerprint-Resistant (Anti-Fingerprint)
This is the final process for all treatments, applying a transparent nano-oil on the surface to create a protective layer. It is not suitable for high-temperature environments.
(12)Embossing
This process uses an engraved roller to press patterns into stainless steel coils, creating a textured surface similar to etching but with smoother edges.