Alloy pipe is a kind of seamless pipe, and its performance is much higher than that of ordinary seamless steel pipe. Because this kind of steel pipe contains more Cr, its high temperature resistance, low temperature resistance and corrosion resistance are not comparable to ordinary seamless steel pipes. Therefore, alloy tubes are widely used in petroleum, aerospace, chemical, electric power, boiler, military and other industries.
Alloy steel pipes are mainly used for high-pressure and high-temperature pipelines and equipment such as power plants, nuclear power plants, high-pressure boilers, high-temperature superheaters and reheaters. It is made of high-quality carbon steel, alloy structural steel and stainless heat-resistant steel, and is made by hot rolling (extrusion, expansion) or cold rolling (pulling).
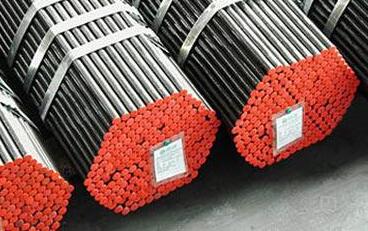
Rust removal of alloy pipe
1. Derusting level. For the construction process of epoxy, vinyl, phenolic and other anti-corrosion coatings commonly used in alloy pipes, it is generally required to make the surface of alloy pipes reach near-white level. It has been proven in practice that almost all scale can be removed with this rust removal grade. Rust and other dirt fully meet the adhesion requirements of the anti-corrosion layer and the alloy pipe, and the spray derusting process can stably and reliably make the quality reach the near-white level at a relatively low cost.
2. In order to achieve the ideal effect of rust removal, it is necessary to select abrasives according to the hardness of the alloy tube surface, the degree of original rust, the required surface roughness, and the type of coating. Single-layer epoxy, two-layer or three-layer polyethylene coating, in order to achieve the desired rust removal effect, a mixed abrasive of steel grit and steel shot is required. Because the steel shot has the effect of strengthening the steel surface, and the steel grit has the effect of etching the steel surface.
3. In order to obtain better uniform cleanliness and roughness distribution, the design of the particle size and proportion of the abrasive is very important. Because the roughness is too large, it is easy to cause the anti-corrosion layer to become thinner at the peak of the anchor pattern. At the same time, because the anchor pattern is too deep, it is easy to form bubbles during the anti-corrosion process, which seriously affects the performance of the anti-corrosion layer. (In actual operation, the ideal ratio of steel grit and steel shot in the abrasive is difficult to achieve).
4. Before the spray treatment, remove the grease and scale on the surface of the alloy tube, and preheat the tube body to 40-60 degrees Celsius with a heating furnace to keep the surface of the alloy tube dry. Because the surface of the alloy tube is free of dirt such as grease, this can enhance the effect of rust removal. In addition, the dry surface of the alloy pipe is also conducive to the separation of steel shot, steel grit, rust and scale, so that the surface of the alloy pipe after derusting will be cleaner.
Alloy steel pipes are mainly used for high-pressure and high-temperature pipelines and equipment such as power plants, nuclear power plants, high-pressure boilers, high-temperature superheaters and reheaters. It is made of high-quality carbon steel, alloy structural steel and stainless heat-resistant steel, and is made by hot rolling (extrusion, expansion) or cold rolling (pulling).
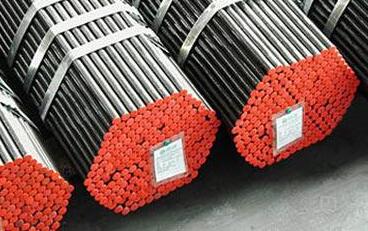
Rust removal of alloy pipe
1. Derusting level. For the construction process of epoxy, vinyl, phenolic and other anti-corrosion coatings commonly used in alloy pipes, it is generally required to make the surface of alloy pipes reach near-white level. It has been proven in practice that almost all scale can be removed with this rust removal grade. Rust and other dirt fully meet the adhesion requirements of the anti-corrosion layer and the alloy pipe, and the spray derusting process can stably and reliably make the quality reach the near-white level at a relatively low cost.
2. In order to achieve the ideal effect of rust removal, it is necessary to select abrasives according to the hardness of the alloy tube surface, the degree of original rust, the required surface roughness, and the type of coating. Single-layer epoxy, two-layer or three-layer polyethylene coating, in order to achieve the desired rust removal effect, a mixed abrasive of steel grit and steel shot is required. Because the steel shot has the effect of strengthening the steel surface, and the steel grit has the effect of etching the steel surface.
3. In order to obtain better uniform cleanliness and roughness distribution, the design of the particle size and proportion of the abrasive is very important. Because the roughness is too large, it is easy to cause the anti-corrosion layer to become thinner at the peak of the anchor pattern. At the same time, because the anchor pattern is too deep, it is easy to form bubbles during the anti-corrosion process, which seriously affects the performance of the anti-corrosion layer. (In actual operation, the ideal ratio of steel grit and steel shot in the abrasive is difficult to achieve).
4. Before the spray treatment, remove the grease and scale on the surface of the alloy tube, and preheat the tube body to 40-60 degrees Celsius with a heating furnace to keep the surface of the alloy tube dry. Because the surface of the alloy tube is free of dirt such as grease, this can enhance the effect of rust removal. In addition, the dry surface of the alloy pipe is also conducive to the separation of steel shot, steel grit, rust and scale, so that the surface of the alloy pipe after derusting will be cleaner.