In the realm of construction, the choice of materials can significantly impact the longevity and resilience of structures. One such material that has been a subject of debate is the steel beam, specifically the H-beam variant. The question often arises: should steel beams be galvanised? This article delves into the advantages of galvanised steel H-beams, drawing from reputable sources and industry insights.
Steel H-beams, also known as "metal H-beams," are structural elements commonly used in construction for their high strength-to-weight ratio. They are characterized by their 'H' shaped cross-section, which provides exceptional load-bearing capabilities. However, steel's susceptibility to corrosion poses a challenge, prompting the question of galvanisation.
The advantages of hot-dip galvanizing of Steel H-Beams are long-term anti-corrosion and wide adaptability to the environment. It is a popular anti-corrosion treatment method. Its advantages are as follows:
The hardness of the galvanized layer is greater than that of steel.
In the corner area, the zinc layer is often thicker than other places, and has good toughness and wear resistance. Other coatings are often the thinnest, most difficult to apply and most vulnerable to damage at these corners, so they often need to be maintained.
Galvanizing provides double protection for steel beams: on the one hand, it forms a barrier to prevent corrosion; on the other hand, it uses sacrificial anodes. Even if the zinc layer is partially detached due to mechanical damage or other reasons, exposing the iron substrate, the surrounding zinc layer can still immediately play a role and protect the steel from corrosion. In contrast, once other types of coatings are damaged, rust will quickly form and spread under the coating, causing the coating to peel off, which is completely different from the protective effect of galvanizing.
The zinc layer is consumed slowly in the atmosphere, and its corrosion rate is much lower than that of steel, about 1/17 to 1/18 of the corrosion rate of steel, making the service life of the zinc layer far longer than other coatings. The thickness of the electroplated zinc layer is generally 5 to 15 microns, while the hot-dip galvanized layer is thicker, usually exceeding 35 microns, and sometimes even reaching 200 microns. Hot-dip galvanizing is superior in protection performance due to its excellent covering ability and dense coating without impurities. The protective film on the surface of the zinc layer is composed of zinc oxide, zinc hydroxide and basic zinc carbonate, which can effectively slow down the corrosion of zinc. Even if the protective film is damaged, a new film layer will form quickly. When the zinc layer is severely damaged and the iron matrix is exposed, zinc provides protection through electrochemical action to form a micro-battery, in which zinc is sacrificed as the anode and iron is protected as the cathode. Due to the difference in standard potential between zinc and iron, hot-dip galvanizing performs better than electroplating in terms of atmospheric corrosion resistance.
The anti-corrosion life of hot-dip galvanizing varies with environmental differences: 13 years in heavy industrial areas, 50 years in marine environments, more than 104 years in suburban environments, and 30 years in urban environments. The anti-corrosion life of the coating is mainly affected by its thickness, which is proportional to the thickness of the steel. Therefore, in the same steel structure, the thicker steel part will receive a thicker coating to ensure a longer anti-corrosion life.
Galvanised steel H-beams are widely used in various applications, including:
The decision to galvanise steel H-beams should be based on the specific requirements of the project, considering factors such as the environment, expected lifespan, and aesthetic preferences.
1.Understanding Steel H-Beams
Steel H-beams, also known as "metal H-beams," are structural elements commonly used in construction for their high strength-to-weight ratio. They are characterized by their 'H' shaped cross-section, which provides exceptional load-bearing capabilities. However, steel's susceptibility to corrosion poses a challenge, prompting the question of galvanisation.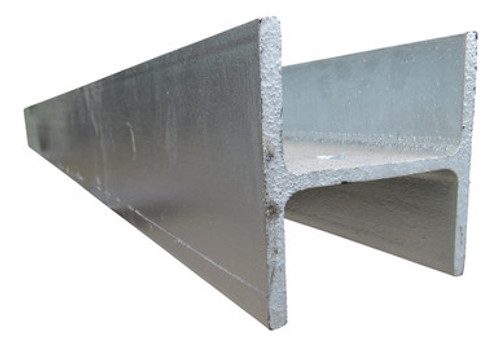