Boiler tubes are a type of seamless tubes. The manufacturing method is the same as that of the seamless pipe, but there are strict requirements on the steel type used in the manufacture of the steel pipe. According to the use temperature, it is divided into two types: general boiler tube and high pressure boiler tube. Production methods include hot rolling, cold rolling (cold drawing)
Defects prone to occur after straightening of hot-rolled boiler tubes and their treatment methods
The straightness of the steel pipe body after straightening of the hot-rolled boiler pipe does not meet the requirements
1. Reason analysis: (1) The deflection value is too large or too small. 2) The amount of depression is too small.
2. Treatment method: (1) Select the correct reduction and deflection value according to the specification, material and bending degree of the hot-rolled boiler tube. 2) If the bending degree of the boiler tube after straightening is greater than that of the incoming material, the deflection value is too large. If the bending degree after straightening is smaller than the bending degree of the incoming material (the straightness is not up to the standard), the deflection value is too small.
After the hot-rolled boiler tube is straightened, the bending degree of the tube head exceeds the standard, and the tube body does not exceed the standard.
1. Reason analysis: (1) The amount of depression is not enough. (2) The exit roller closes slowly.
2. Treatment method: (1) Adjust the appropriate reduction amount. (2) Adjust the closing delay of the exit roller to reduce the blind area of straightening.
Hot Rolled Boiler Tube Tube Head Flattening
1. Cause analysis: (1) The straightening rollers are closed too early, causing damage to the pipe head. (2) The amount of depression is too large.
2. Treatment method: (1) Adjust the closing delay of the straightening roller. (2) Reduce the reduction of the straightening roller.
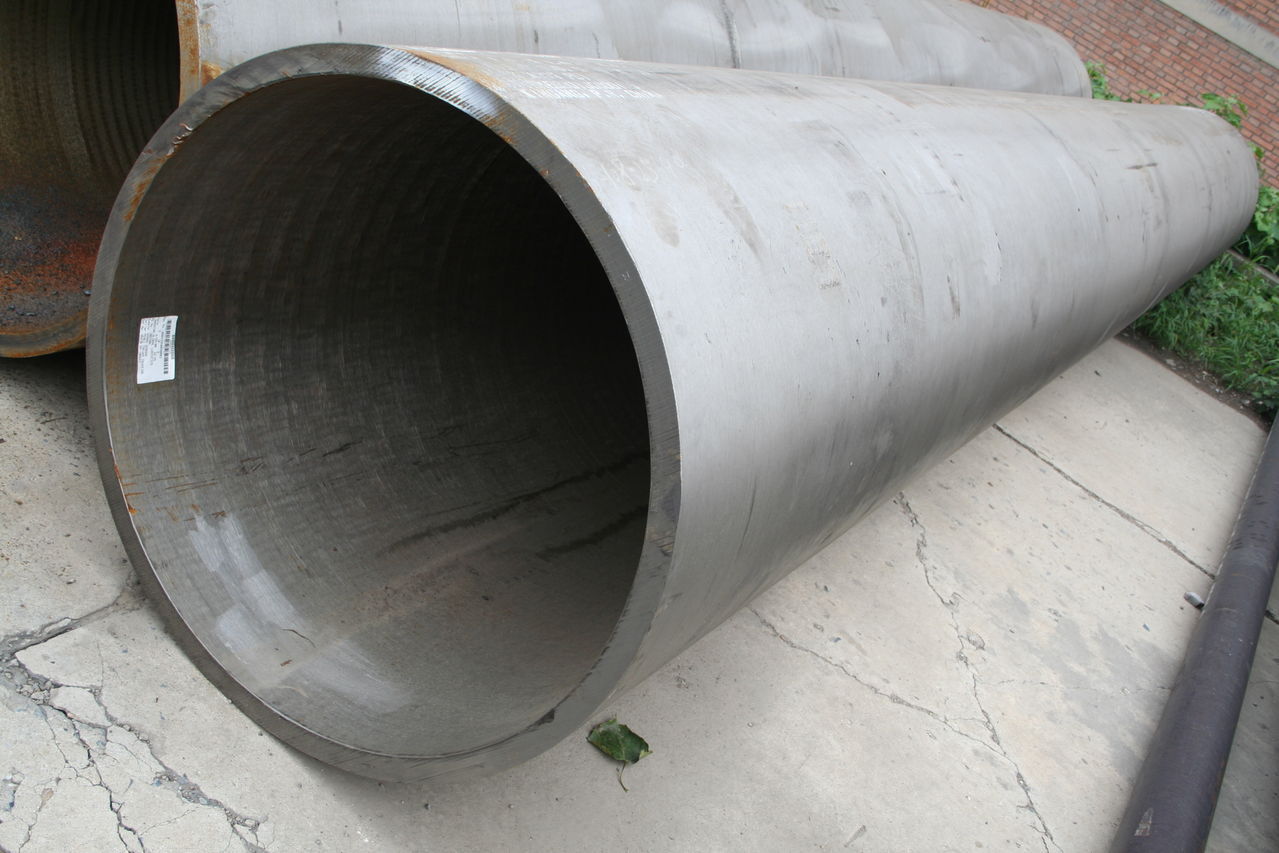
Hot-rolled boiler tube tail bruising
1. Cause analysis: (1)) The deflection value is too large. (2) The angle of the upper roller at the entrance is too small. (3) Adjust the opening delay of the middle roller.
2. Treatment method: (1) Reduce the deflection value. If the bending of the incoming material is large, appropriately increase the reduction of the exit roller and the middle roller. (2) Appropriately increase the angle of the upper roller at the entrance.
Hot Rolled Boiler Tube Tube Body Track Correction
1. Cause analysis: (1) The angle of the straightening roller is too small or too large. (2) The straightening roller has no reduction.
2. Treatment method: (1) Properly adjust the angle of the straightening roller (find out the straightening roller that produces straightening marks). (2) Properly adjust the reduction of the straightening roller.
Scratches on the hot-rolled boiler tube body.
1. Reason analysis: (1) The entry and exit roadways are due to residual sawdust. (2) The burr at the end of the pipe will cause damage to the inner lining of the roadway, causing the pipe body to be scratched.
2. Treatment method: (1) Clean up the residual sawdust in the roadway, and grind the scratched lining board. (2) Replace the saw blade in time to reduce the burrs at the pipe end.
The hot-rolled boiler tube outlet roadway liner interface caused damage to the tube head.
1. Cause analysis: The interface of the lining plate is dislocated, and the hot-rolled boiler tube shakes in the exit roadway, causing damage to the tube head.
2. Treatment method: (1) Grinding and finishing the lining board of the exit roadway. (2) Adjust the straightening parameters (such as increasing the deflection value, increasing the outlet reduction, etc.) to reduce the shaking of the boiler tube.
The surface of the hot-rolled boiler tube body is crushed.
1. Cause analysis: After the side door of the exit passage was opened, two steel pipes were on it due to the problem of the L-shaped material receiving hook and the sensing element. After the passage side door is closed, it presses on the second boiler tube, causing the tube body to be crushed.
2. Treatment method: Adjust the position and sensitivity of the sensing element due to the L-shaped hook.
Defects prone to occur after straightening of hot-rolled boiler tubes and their treatment methods
The straightness of the steel pipe body after straightening of the hot-rolled boiler pipe does not meet the requirements
1. Reason analysis: (1) The deflection value is too large or too small. 2) The amount of depression is too small.
2. Treatment method: (1) Select the correct reduction and deflection value according to the specification, material and bending degree of the hot-rolled boiler tube. 2) If the bending degree of the boiler tube after straightening is greater than that of the incoming material, the deflection value is too large. If the bending degree after straightening is smaller than the bending degree of the incoming material (the straightness is not up to the standard), the deflection value is too small.
After the hot-rolled boiler tube is straightened, the bending degree of the tube head exceeds the standard, and the tube body does not exceed the standard.
1. Reason analysis: (1) The amount of depression is not enough. (2) The exit roller closes slowly.
2. Treatment method: (1) Adjust the appropriate reduction amount. (2) Adjust the closing delay of the exit roller to reduce the blind area of straightening.
Hot Rolled Boiler Tube Tube Head Flattening
1. Cause analysis: (1) The straightening rollers are closed too early, causing damage to the pipe head. (2) The amount of depression is too large.
2. Treatment method: (1) Adjust the closing delay of the straightening roller. (2) Reduce the reduction of the straightening roller.
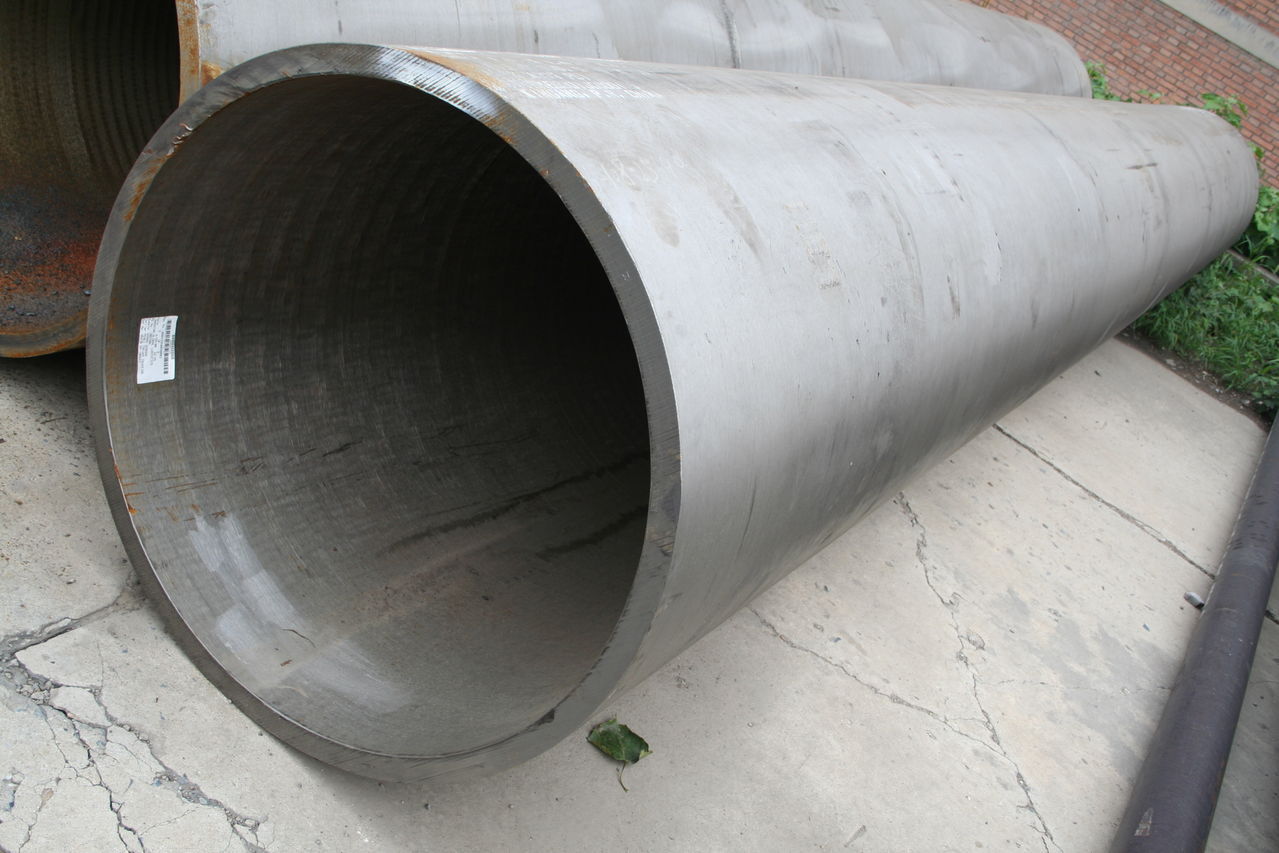
Hot-rolled boiler tube tail bruising
1. Cause analysis: (1)) The deflection value is too large. (2) The angle of the upper roller at the entrance is too small. (3) Adjust the opening delay of the middle roller.
2. Treatment method: (1) Reduce the deflection value. If the bending of the incoming material is large, appropriately increase the reduction of the exit roller and the middle roller. (2) Appropriately increase the angle of the upper roller at the entrance.
Hot Rolled Boiler Tube Tube Body Track Correction
1. Cause analysis: (1) The angle of the straightening roller is too small or too large. (2) The straightening roller has no reduction.
2. Treatment method: (1) Properly adjust the angle of the straightening roller (find out the straightening roller that produces straightening marks). (2) Properly adjust the reduction of the straightening roller.
Scratches on the hot-rolled boiler tube body.
1. Reason analysis: (1) The entry and exit roadways are due to residual sawdust. (2) The burr at the end of the pipe will cause damage to the inner lining of the roadway, causing the pipe body to be scratched.
2. Treatment method: (1) Clean up the residual sawdust in the roadway, and grind the scratched lining board. (2) Replace the saw blade in time to reduce the burrs at the pipe end.
The hot-rolled boiler tube outlet roadway liner interface caused damage to the tube head.
1. Cause analysis: The interface of the lining plate is dislocated, and the hot-rolled boiler tube shakes in the exit roadway, causing damage to the tube head.
2. Treatment method: (1) Grinding and finishing the lining board of the exit roadway. (2) Adjust the straightening parameters (such as increasing the deflection value, increasing the outlet reduction, etc.) to reduce the shaking of the boiler tube.
The surface of the hot-rolled boiler tube body is crushed.
1. Cause analysis: After the side door of the exit passage was opened, two steel pipes were on it due to the problem of the L-shaped material receiving hook and the sensing element. After the passage side door is closed, it presses on the second boiler tube, causing the tube body to be crushed.
2. Treatment method: Adjust the position and sensitivity of the sensing element due to the L-shaped hook.