What is welding slag inclusion?
Welded pipe slag inclusions are slag that remains inside the weld. Welding slag inclusions are generally divided into two categories:
The first category is metal slag inclusions. The second category is non-metallic slag, which refers to the slag remaining in the weld after welding, including electrode coating or flux, sulfide, oxide and nitride. According to its formation, it can be divided into point-like slag inclusions, linear slag inclusions, chain-like slag inclusions and dense slag inclusions.
Slag inclusions will reduce the plasticity and toughness of steel pipe welds, and slag inclusions with sharp corners will cause stress concentration at the tip, and the tip will develop into a crack source, especially in welds with a large tendency to air quenching. Under the action of stress on the steel pipe, cracks will first appear at the slag inclusions in the weld and develop along the way, resulting in a decrease in strength and cracking of the weld.
There are many factors for the formation of welding slag inclusions. If there are many inclusions in the welded steel pipe, it will inevitably cause inclusions in the weld. In addition, process factors also have a great influence on welding slag inclusions.
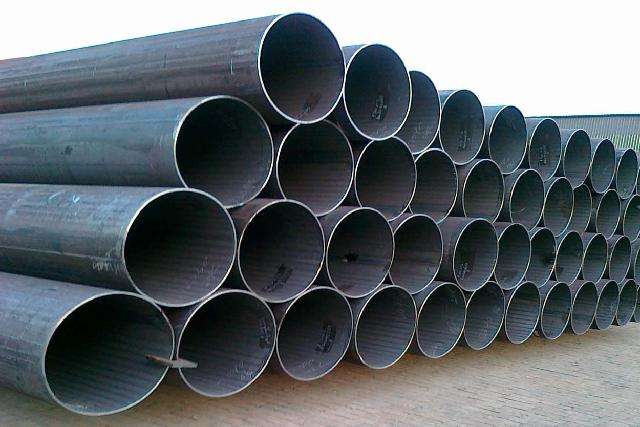
Causes of welding slag inclusions
1. The slag between the edge of the welded steel pipe, the weld layer and the weld bead has not been cleaned. Especially when using basic electrodes, if the slag is not removed, slag inclusions are more likely to occur;
2. The welding current is too small. The heat obtained by melting metal and slag is insufficient, which reduces its fluidity, and the molten metal solidifies quickly, and the slag has no time to float out.
3. The chemical composition of the base metal and the welding material is improper
Methods to prevent inclusions in welds
1. Use pipes with good process performance, and prohibit the use of pipes that are expired, deteriorated or have defects in appearance;
2. Before welding, clean up the rust, oil and other harmful impurities in the welding area. The groove angle should not be too small, and the slag in the groove, on both sides, and between layers must be cleaned.
3. Select reasonable welding process parameters through welding process uation, and select welding rods with appropriate diameters according to the thickness of steel pipes. According to the flow direction of the slag, adjust the angle of the electrode and the method of transporting the electrode at any time, so that the slag can float to the surface of the molten pool smoothly.
Welded pipe slag inclusions are slag that remains inside the weld. Welding slag inclusions are generally divided into two categories:
The first category is metal slag inclusions. The second category is non-metallic slag, which refers to the slag remaining in the weld after welding, including electrode coating or flux, sulfide, oxide and nitride. According to its formation, it can be divided into point-like slag inclusions, linear slag inclusions, chain-like slag inclusions and dense slag inclusions.
Slag inclusions will reduce the plasticity and toughness of steel pipe welds, and slag inclusions with sharp corners will cause stress concentration at the tip, and the tip will develop into a crack source, especially in welds with a large tendency to air quenching. Under the action of stress on the steel pipe, cracks will first appear at the slag inclusions in the weld and develop along the way, resulting in a decrease in strength and cracking of the weld.
There are many factors for the formation of welding slag inclusions. If there are many inclusions in the welded steel pipe, it will inevitably cause inclusions in the weld. In addition, process factors also have a great influence on welding slag inclusions.
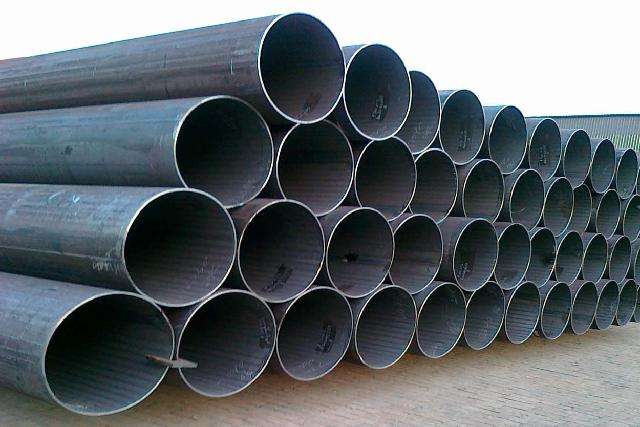
Causes of welding slag inclusions
1. The slag between the edge of the welded steel pipe, the weld layer and the weld bead has not been cleaned. Especially when using basic electrodes, if the slag is not removed, slag inclusions are more likely to occur;
2. The welding current is too small. The heat obtained by melting metal and slag is insufficient, which reduces its fluidity, and the molten metal solidifies quickly, and the slag has no time to float out.
3. The chemical composition of the base metal and the welding material is improper
Methods to prevent inclusions in welds
1. Use pipes with good process performance, and prohibit the use of pipes that are expired, deteriorated or have defects in appearance;
2. Before welding, clean up the rust, oil and other harmful impurities in the welding area. The groove angle should not be too small, and the slag in the groove, on both sides, and between layers must be cleaned.
3. Select reasonable welding process parameters through welding process uation, and select welding rods with appropriate diameters according to the thickness of steel pipes. According to the flow direction of the slag, adjust the angle of the electrode and the method of transporting the electrode at any time, so that the slag can float to the surface of the molten pool smoothly.