During the forming process of the spiral submerged arc welded pipe(SSAW pipe), the wrong edge, the thickness of the edge of the plate, the change of the gap between the forming seam and the swing of the bridge, etc., will affect the welding quality and cause defects such as inclusions and pores. When producing thick-walled spiral submerged arc welded pipes, inclusions and pores are more likely to occur than thin-walled submerged arc welded pipes. The inclusions and pores in the weld weaken the effective working cross-sectional area of the weld, reduce the plasticity and toughness of the welded joint, and thus reduce the expected performance of the steel pipe.
Method of Preventing Weld Seam Inclusion of Spiral Submerged Arc Welded Pipe
(1) Strictly control the quality of raw materials such as strip steel and welding wire, and strictly control the content of inclusions. Do a good job in the storage of welding wire and coil to avoid oil stains and rust; dry the flux strictly according to the process requirements, and keep the flux clean and uniform in particle size.
(2) Avoid artificial hard bending, reduce the change of raw material width and delivery position, adjust the position of the vertical roller in time, make the edge of the strip steel flat, no extrusion or minimize extrusion, so as to stabilize the forming and ensure a good forming seam state .
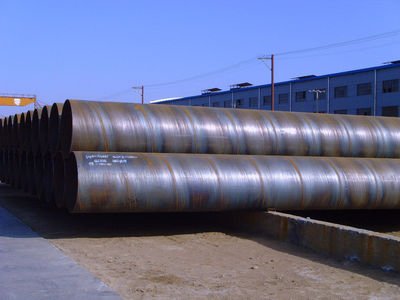
(3) Reasonably adjust the side clearance and overlap of the disc shear blades, and replace the blunt shear blades in time to ensure that the disc shears are in good working condition, so that there are no steps, slopes, etc. on the edge of the board. Reasonably adjust the height of the welding pad roller to avoid the phenomenon of outer tightness and inner looseness of the forming seam caused by the excessive height of the welding pad roller.
(4) For the production of thick-walled spiral submerged arc welded pipes, select the appropriate groove form and groove angle, and use a double milling device that trims the edge first and then mills the edge or rough milling and fine milling. It can improve the processing accuracy of the edge of the board and improve the state of the forming seam.
(5) Choose reasonable welding process parameters, maintain a good weld shape coefficient, and avoid narrow and deep seam gaps. When conditions permit, use as much heat as possible for welding to ensure the slow cooling of the molten pool, increase the agitation of the molten pool, and promote the surfacing of gases and other reactants in the molten pool.
(6) Adjust the position of the internal welding spot so that the welding spot deviates from the occlusal area and is in a stable seam state, so as to reduce the influence of the joint formation of the occlusal area on the internal welding.
(7) Adjust the position where the flux is fed. It is best to make the flux supply port close to the solder joint to reduce the chance of flux entering the forming seam.
Method of Preventing Weld Seam Inclusion of Spiral Submerged Arc Welded Pipe
(1) Strictly control the quality of raw materials such as strip steel and welding wire, and strictly control the content of inclusions. Do a good job in the storage of welding wire and coil to avoid oil stains and rust; dry the flux strictly according to the process requirements, and keep the flux clean and uniform in particle size.
(2) Avoid artificial hard bending, reduce the change of raw material width and delivery position, adjust the position of the vertical roller in time, make the edge of the strip steel flat, no extrusion or minimize extrusion, so as to stabilize the forming and ensure a good forming seam state .
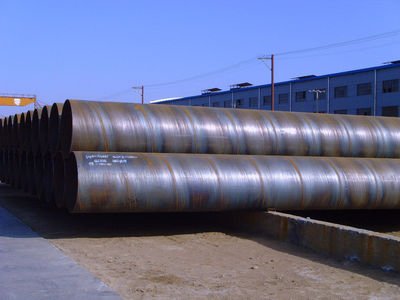
(3) Reasonably adjust the side clearance and overlap of the disc shear blades, and replace the blunt shear blades in time to ensure that the disc shears are in good working condition, so that there are no steps, slopes, etc. on the edge of the board. Reasonably adjust the height of the welding pad roller to avoid the phenomenon of outer tightness and inner looseness of the forming seam caused by the excessive height of the welding pad roller.
(4) For the production of thick-walled spiral submerged arc welded pipes, select the appropriate groove form and groove angle, and use a double milling device that trims the edge first and then mills the edge or rough milling and fine milling. It can improve the processing accuracy of the edge of the board and improve the state of the forming seam.
(5) Choose reasonable welding process parameters, maintain a good weld shape coefficient, and avoid narrow and deep seam gaps. When conditions permit, use as much heat as possible for welding to ensure the slow cooling of the molten pool, increase the agitation of the molten pool, and promote the surfacing of gases and other reactants in the molten pool.
(6) Adjust the position of the internal welding spot so that the welding spot deviates from the occlusal area and is in a stable seam state, so as to reduce the influence of the joint formation of the occlusal area on the internal welding.
(7) Adjust the position where the flux is fed. It is best to make the flux supply port close to the solder joint to reduce the chance of flux entering the forming seam.