Submerged arc welded steel pipe (LSAW pipe or SSAW pipe) weld surface indentation refers to a weld defect in which the weld surface is partially lower than the normal surface of the weld, and is a common weld surface defect in submerged arc welding. In the production of submerged arc welded steel pipes, the weld seam is usually relatively long. Especially in the production of one-step spiral submerged arc welded steel pipes, it is often the case that thousands of meters of submerged arc welds are welded at one time, so it is relatively easy to produce pits on the surface of the weld.
Hazards of indentation on weld surface
1. If the depth of the indentation on the surface of the weld is >1.5mm, it must be treated as a weld defect. Once a steel pipe has several weld pits lower than the base metal, it is easy to cause the steel pipe to be degraded or even scrapped, and at least it will increase the repair cost of the steel pipe production.
2. Due to the wide application of 3PE external anti-corrosion technology for dry steel pipes and the influence of weld seam height on the thinning of the anti-corrosion layer, the current submerged arc welded steel pipe requires the welding front height to be as low as possible to save anti-corrosion costs as much as possible. In actual production, some steel pipe manufacturers have controlled the reinforcement of the outer weld to ≤1mm on the premise that it is not lower than the surface of the base metal of the steel pipe. At this time, if the depth of the indentation on the surface of the weld is > 1mm, the weld will be lower than the base metal, resulting in serious weld defects.
3. For submerged arc welded steel pipes that are subject to internal powder spraying and external 3PE anti-corrosion, anti-corrosion defects such as leaks or 3PE anti-corrosion bubbles are prone to occur at the pits on the weld surface, which will affect the anti-corrosion quality of the steel tubes.
Factors Affecting Creation of Pressure Pit
From the formation process of indentation, it can be seen that the more gas generated in the weld pool, the easier it is to produce weld indentation. The greater the resistance of the flux layer and slag to gas escape, the more difficult it is for gas to escape, and the easier it is to produce pressure pits.
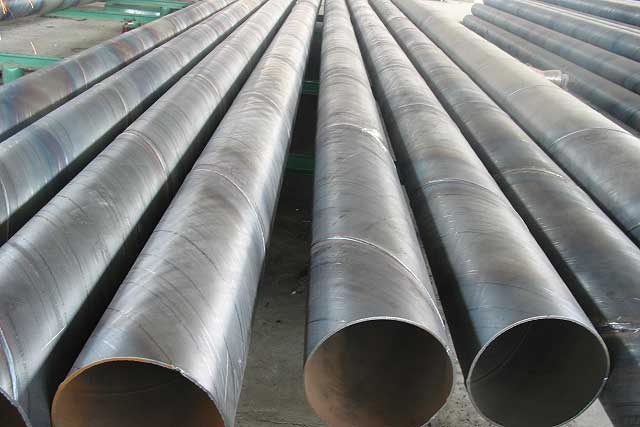
Measures to prevent weld pitting
1. Choose the right flux:
Under the premise of ensuring the internal quality of the weld, flux with low oxidation, low viscosity, low surface tension and low bulk density should be selected. In addition, in order to improve the ventilation of the flux, the flux with a smaller particle mat should be selected, especially in high-current welding. The particles of the flux should be as uniform as possible, and the particle size is generally controlled at 10-60 mesh. It is not allowed to mix coarse-grained flux and flux that is too fine. For the flux used in steel pipe submerged arc welding, it is necessary to ensure that the fine flux can be sucked away by the flux recovery system to ensure that the particle size of the flux is relatively uniform.
2. Proper use of flux:
The flux should be kept clean during use, without rust, dust, iron oxide and other impurities. The iron oxide in the flux must be removed by magnetic separation for recycled or recovered flux. The flux should be dried according to the specified temperature before use to ensure the moisture content in the flux. Generally, the moisture content in the flux should be ≤0.1%
3 Reasonable selection of tube blank and welding wire:
In terms of material selection, try to choose tube blanks and welding wires with low C, O, N, H and other elements to reduce the generation of gas during welding
4. Reasonable selection of welding parameters:
Under the premise of ensuring the quality of the weld seam, the use of a smaller welding current can reduce the generation of gas and reduce welding pressure pits. Appropriately increasing the arc voltage can increase the arc cavity, make the layers of welding slag thinner, and reduce the resistance of gas escape and bubble pressure in the arc cavity, which is beneficial to reduce weld pitting. Reducing welding speed can increase the existence time of liquid molten pool and low viscosity slag, which is conducive to gas escape and reduces pitting.
5. Maintain a reasonable welding inclination:
Increasing the angle of downhill welding will thin the slag layer due to the flow of slag, which is beneficial to reduce pitting. In the submerged arc welding steel pipe welding, the eccentric distance and the inclination angle of welding wire can be adjusted reasonably to ensure welding at the best angle, reduce and prevent weld pitting.
Hazards of indentation on weld surface
1. If the depth of the indentation on the surface of the weld is >1.5mm, it must be treated as a weld defect. Once a steel pipe has several weld pits lower than the base metal, it is easy to cause the steel pipe to be degraded or even scrapped, and at least it will increase the repair cost of the steel pipe production.
2. Due to the wide application of 3PE external anti-corrosion technology for dry steel pipes and the influence of weld seam height on the thinning of the anti-corrosion layer, the current submerged arc welded steel pipe requires the welding front height to be as low as possible to save anti-corrosion costs as much as possible. In actual production, some steel pipe manufacturers have controlled the reinforcement of the outer weld to ≤1mm on the premise that it is not lower than the surface of the base metal of the steel pipe. At this time, if the depth of the indentation on the surface of the weld is > 1mm, the weld will be lower than the base metal, resulting in serious weld defects.
3. For submerged arc welded steel pipes that are subject to internal powder spraying and external 3PE anti-corrosion, anti-corrosion defects such as leaks or 3PE anti-corrosion bubbles are prone to occur at the pits on the weld surface, which will affect the anti-corrosion quality of the steel tubes.
Factors Affecting Creation of Pressure Pit
From the formation process of indentation, it can be seen that the more gas generated in the weld pool, the easier it is to produce weld indentation. The greater the resistance of the flux layer and slag to gas escape, the more difficult it is for gas to escape, and the easier it is to produce pressure pits.
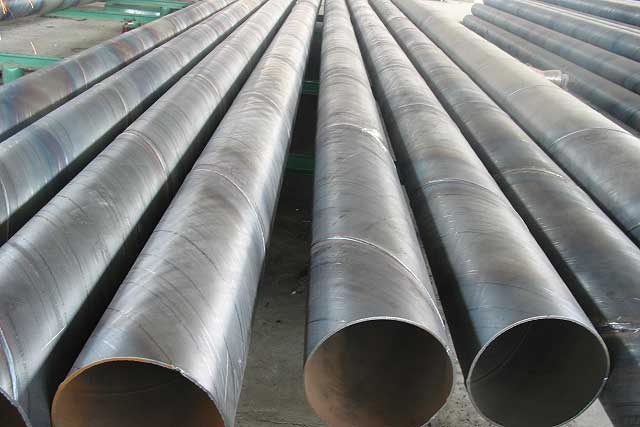
Measures to prevent weld pitting
1. Choose the right flux:
Under the premise of ensuring the internal quality of the weld, flux with low oxidation, low viscosity, low surface tension and low bulk density should be selected. In addition, in order to improve the ventilation of the flux, the flux with a smaller particle mat should be selected, especially in high-current welding. The particles of the flux should be as uniform as possible, and the particle size is generally controlled at 10-60 mesh. It is not allowed to mix coarse-grained flux and flux that is too fine. For the flux used in steel pipe submerged arc welding, it is necessary to ensure that the fine flux can be sucked away by the flux recovery system to ensure that the particle size of the flux is relatively uniform.
2. Proper use of flux:
The flux should be kept clean during use, without rust, dust, iron oxide and other impurities. The iron oxide in the flux must be removed by magnetic separation for recycled or recovered flux. The flux should be dried according to the specified temperature before use to ensure the moisture content in the flux. Generally, the moisture content in the flux should be ≤0.1%
3 Reasonable selection of tube blank and welding wire:
In terms of material selection, try to choose tube blanks and welding wires with low C, O, N, H and other elements to reduce the generation of gas during welding
4. Reasonable selection of welding parameters:
Under the premise of ensuring the quality of the weld seam, the use of a smaller welding current can reduce the generation of gas and reduce welding pressure pits. Appropriately increasing the arc voltage can increase the arc cavity, make the layers of welding slag thinner, and reduce the resistance of gas escape and bubble pressure in the arc cavity, which is beneficial to reduce weld pitting. Reducing welding speed can increase the existence time of liquid molten pool and low viscosity slag, which is conducive to gas escape and reduces pitting.
5. Maintain a reasonable welding inclination:
Increasing the angle of downhill welding will thin the slag layer due to the flow of slag, which is beneficial to reduce pitting. In the submerged arc welding steel pipe welding, the eccentric distance and the inclination angle of welding wire can be adjusted reasonably to ensure welding at the best angle, reduce and prevent weld pitting.