The production process of hot-rolled seamless steel pipe is a complex thermal processing process, which transforms solid tube into hollow steel pipe. Nansteel Manufacturing Co., Ltd carefully summarizes the detailed steps of the production process of hot-rolled seamless steel pipe:
1. Tube preparation
Selecting tube billets: Round ingots, rolled billets or continuous casting tube billets are usually used as raw materials. The quality of the tube billets directly affects the quality of the final steel pipe, so strict control is required.
Inspection and cleaning: Perform visual inspection on the tube billets to remove surface defects such as cracks, inclusions, etc.
Cutting: Cut the tube billets into the required length for subsequent heating and perforation.
2. Tube heating
Heating furnace: The cut tube billet is sent into the heating furnace for heating. There are many types of heating furnaces, such as ring furnaces, stepping furnaces, etc.
Heating temperature: The tube billet is heated to the appropriate rolling temperature, usually between 1100-1300℃. The control of heating temperature is very important. Too high will lead to overburning, and too low will increase the difficulty of rolling.
Uniform heating: Ensure that the temperature inside and outside the tube billet is uniform to ensure smooth piercing and rolling.
3. Piercing
Punching machine: The heated tube is sent to the punching machine for punching, so that a cavity is formed inside the solid tube, which becomes a rough tube.
Punching method: Commonly used punching methods include oblique rolling punching and push rolling punching. Oblique rolling punching is the most widely used punching method at present. It uses the rotation of the roller and the axial movement of the tube to form a hole in the center of the tube.
Punching head: During the punching process, the role of the jack is to support the inside of the tube, control the inner diameter size, and prevent the center of the tube from collapsing.
Punching requirements: The rough tube after punching requires uniform wall thickness, smooth inner and outer surfaces, and no defects such as cracks and folds.
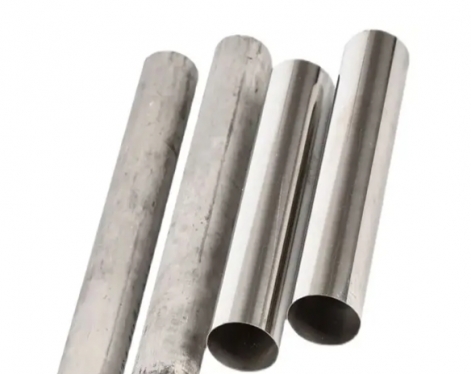
4. Rolling
Tube rolling mill: The perforated rough tube is sent to the tube rolling mill for further rolling to reduce the wall thickness and outer diameter to reach the required size.
Tube rolling method: Commonly used tube rolling methods include automatic tube rolling mill, continuous tube rolling mill, periodic tube rolling mill, etc.
Automatic tube rolling mill: It uses conical rollers to roll through the rotation of the rollers and the axial movement of the tube blank.
Continuous tube rolling mill: It consists of multiple rolling mills, and the rough tube is rolled through each rolling mill in turn to achieve continuous production.
Rolling process: During the rolling process, the tube blank rotates and moves forward continuously, and plastic deformation occurs under the action of the rollers, the wall thickness gradually decreases, and the outer diameter gradually approaches the finished product size.
5. Scaling and sizing
Scaling: The wall thickness of the rolled steel pipe is leveled by a leveling machine to further improve the wall thickness accuracy.
Sizing: The outer diameter of the steel pipe is precisely controlled by a sizing machine to meet the final specification requirements. Sizing is usually carried out using a stretch reducer or a sizing mill.
6. Cooling
Cooling method: The rolled steel pipe is cooled. Common cooling methods include air cooling and water cooling. Water cooling has a faster cooling speed and can improve the strength and hardness of the steel pipe.
7. Straightening
Straightening machine: Straighten the cooled steel pipe to eliminate bending deformation and ensure the straightness of the steel pipe.
8. Cutting heads and tails of steel pipe
Cutting heads and tails: Cut off the heads and tails at both ends of the steel pipe to remove defects caused by rolling and cooling.
Cutting: Cutting the steel pipe into the required length.
9. Inspection
Nondestructive testing: Conduct nondestructive testing such as water pressure testing, ultrasonic testing, eddy current testing, etc. to check the internal and surface quality of the steel pipe to ensure that there are no defects such as cracks, pores, inclusions, etc.
Other tests: Chemical composition analysis, mechanical properties test and other tests as needed.
10. Marking and storage
Marking: Mark the qualified steel pipes, including specifications, materials, production batch number and other information.
Oil coating: In order to prevent the steel pipes from rusting during storage and transportation, oil is usually applied to the surface.
Packaging: Packaging is carried out according to customer requirements, such as bundling, packing, etc.
Warehousing: The packaged steel pipes are stored in the warehouse.
Conclusion
The production process of hot-rolled seamless steel pipe is a complex process involving multiple processes. Each link has an important impact on the quality of the final product. Through strict control of each link, high-quality hot-rolled seamless steel pipes can be produced to meet the application needs of different industrial fields.
Read more: Hot Rolled Seamless Steel Pipes Main Application Industry
1. Tube preparation
Selecting tube billets: Round ingots, rolled billets or continuous casting tube billets are usually used as raw materials. The quality of the tube billets directly affects the quality of the final steel pipe, so strict control is required.
Inspection and cleaning: Perform visual inspection on the tube billets to remove surface defects such as cracks, inclusions, etc.
Cutting: Cut the tube billets into the required length for subsequent heating and perforation.
2. Tube heating
Heating furnace: The cut tube billet is sent into the heating furnace for heating. There are many types of heating furnaces, such as ring furnaces, stepping furnaces, etc.
Heating temperature: The tube billet is heated to the appropriate rolling temperature, usually between 1100-1300℃. The control of heating temperature is very important. Too high will lead to overburning, and too low will increase the difficulty of rolling.
Uniform heating: Ensure that the temperature inside and outside the tube billet is uniform to ensure smooth piercing and rolling.
3. Piercing
Punching machine: The heated tube is sent to the punching machine for punching, so that a cavity is formed inside the solid tube, which becomes a rough tube.
Punching method: Commonly used punching methods include oblique rolling punching and push rolling punching. Oblique rolling punching is the most widely used punching method at present. It uses the rotation of the roller and the axial movement of the tube to form a hole in the center of the tube.
Punching head: During the punching process, the role of the jack is to support the inside of the tube, control the inner diameter size, and prevent the center of the tube from collapsing.
Punching requirements: The rough tube after punching requires uniform wall thickness, smooth inner and outer surfaces, and no defects such as cracks and folds.
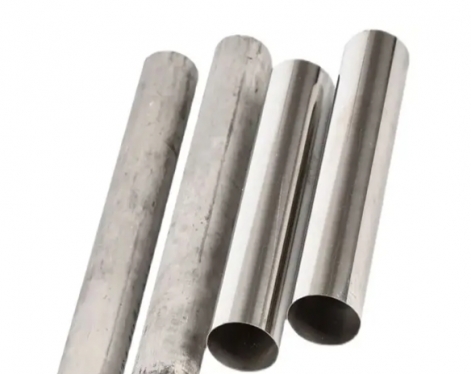
4. Rolling
Tube rolling mill: The perforated rough tube is sent to the tube rolling mill for further rolling to reduce the wall thickness and outer diameter to reach the required size.
Tube rolling method: Commonly used tube rolling methods include automatic tube rolling mill, continuous tube rolling mill, periodic tube rolling mill, etc.
Automatic tube rolling mill: It uses conical rollers to roll through the rotation of the rollers and the axial movement of the tube blank.
Continuous tube rolling mill: It consists of multiple rolling mills, and the rough tube is rolled through each rolling mill in turn to achieve continuous production.
Rolling process: During the rolling process, the tube blank rotates and moves forward continuously, and plastic deformation occurs under the action of the rollers, the wall thickness gradually decreases, and the outer diameter gradually approaches the finished product size.
5. Scaling and sizing
Scaling: The wall thickness of the rolled steel pipe is leveled by a leveling machine to further improve the wall thickness accuracy.
Sizing: The outer diameter of the steel pipe is precisely controlled by a sizing machine to meet the final specification requirements. Sizing is usually carried out using a stretch reducer or a sizing mill.
6. Cooling
Cooling method: The rolled steel pipe is cooled. Common cooling methods include air cooling and water cooling. Water cooling has a faster cooling speed and can improve the strength and hardness of the steel pipe.
7. Straightening
Straightening machine: Straighten the cooled steel pipe to eliminate bending deformation and ensure the straightness of the steel pipe.
8. Cutting heads and tails of steel pipe
Cutting heads and tails: Cut off the heads and tails at both ends of the steel pipe to remove defects caused by rolling and cooling.
Cutting: Cutting the steel pipe into the required length.
9. Inspection
Nondestructive testing: Conduct nondestructive testing such as water pressure testing, ultrasonic testing, eddy current testing, etc. to check the internal and surface quality of the steel pipe to ensure that there are no defects such as cracks, pores, inclusions, etc.
Other tests: Chemical composition analysis, mechanical properties test and other tests as needed.
10. Marking and storage
Marking: Mark the qualified steel pipes, including specifications, materials, production batch number and other information.
Oil coating: In order to prevent the steel pipes from rusting during storage and transportation, oil is usually applied to the surface.
Packaging: Packaging is carried out according to customer requirements, such as bundling, packing, etc.
Warehousing: The packaged steel pipes are stored in the warehouse.
Conclusion
The production process of hot-rolled seamless steel pipe is a complex process involving multiple processes. Each link has an important impact on the quality of the final product. Through strict control of each link, high-quality hot-rolled seamless steel pipes can be produced to meet the application needs of different industrial fields.
Read more: Hot Rolled Seamless Steel Pipes Main Application Industry