Steel pipe welding is a commonly used process in construction, machinery manufacturing, oil, natural gas, hydropower and chemical industries, but the quality of welded steel tubes directly affects the safety and service life of the project. Therefore, the quality of steel pipe welding must undergo strict acceptance.
1. Acceptance criterias for welded tubes
(1)Weld seam forming
The weld seam should be even and continuous, without gaps and black slag inclusions. Both sides of the weld seam should be straight and smooth, with no obvious unevenness, inclusions, subsurface cracks and other defects.
(2)Weld seam appearance
Welded steel tubes should ensure complete penetration, and there should be no missing welds, weak welds, poor local fusion, etc.
(3)Dimensional deviation
When inspecting welded steel tubes, it should be noted that basic deviations such as pipe diameter, wall thickness, tolerances and curvature should meet the requirements of engineering specifications.
(4)Chemical composition
The chemical composition is analyzed and tested, and the steel pipe weld material should meet the chemical composition specifications of the steel.
(5)Mechanical properties
The mechanical properties of welded steel tubes should meet the requirements of national or industry standards. The tensile strength, bending strength and hardness values of the steel pipe weld seams should be tested and the results checked.
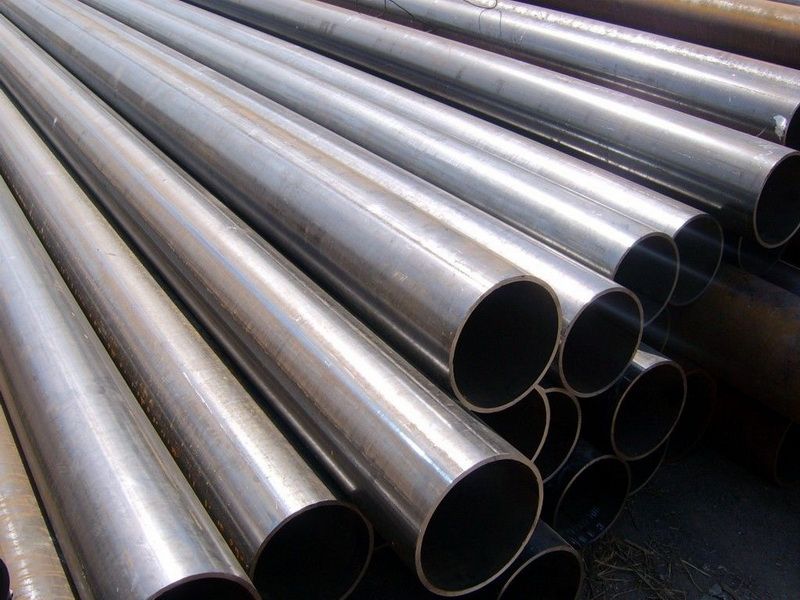
2. Acceptance method of welded tubes
(1) Appearance inspection
Conduct a comprehensive observation and inspection of the weld structure to see whether the direction and size of the weld meet the requirements of the engineering specifications. If there are irregular welds, methods such as sand blasting and chemical cleaning can be used to remove the weld seams.
(2) Non-destructive testing
Non-destructive testing refers to the use of heat, sound, light, electricity and magnetism caused by abnormal internal structure or defects of the material on the premise of inspecting the inside of mechanical materials without damaging or affecting the performance of the object being tested and without damaging the internal organization of the object being tested. and other reaction changes, using physical or chemical methods as a means, and with the help of modern technology and equipment, to analyze the structure and state of the specimen's interior and surface, as well as the type, quantity, shape, nature, location, size, distribution and changes of defects. Methods for conducting inspections and tests. High-precision non-destructive testing technologies such as ultrasonic testing, X-ray testing or magnetic particle testing are used to detect possible defects in the welds. Once discovered, they need to be corrected in time.
(3) Mechanical parameter detection
Standardized testing equipment is used to measure the mechanical properties of electric welded steel pipes from multiple angles to determine whether they meet engineering requirements and standards. Commonly used mechanical property indicators include: strength, plasticity, hardness, impact toughness, fatigue strength, etc.
I believe that through the above introduction and acceptance methods, everyone has a certain understanding of the acceptance of welded steel pipes. During the process, we should be strict about the welding process and always put safety first. At the same time, we should also actively cooperate to carry out acceptance work as early as possible, detect and correct possible defects in a timely manner, and ensure the quality of steel pipe welding and the progress of project construction.
1. Acceptance criterias for welded tubes
(1)Weld seam forming
The weld seam should be even and continuous, without gaps and black slag inclusions. Both sides of the weld seam should be straight and smooth, with no obvious unevenness, inclusions, subsurface cracks and other defects.
(2)Weld seam appearance
Welded steel tubes should ensure complete penetration, and there should be no missing welds, weak welds, poor local fusion, etc.
(3)Dimensional deviation
When inspecting welded steel tubes, it should be noted that basic deviations such as pipe diameter, wall thickness, tolerances and curvature should meet the requirements of engineering specifications.
(4)Chemical composition
The chemical composition is analyzed and tested, and the steel pipe weld material should meet the chemical composition specifications of the steel.
(5)Mechanical properties
The mechanical properties of welded steel tubes should meet the requirements of national or industry standards. The tensile strength, bending strength and hardness values of the steel pipe weld seams should be tested and the results checked.
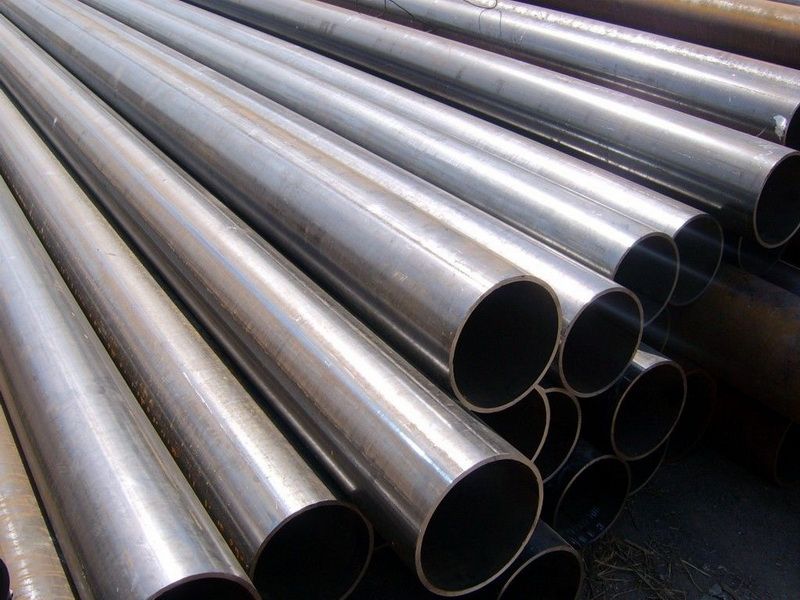
2. Acceptance method of welded tubes
(1) Appearance inspection
Conduct a comprehensive observation and inspection of the weld structure to see whether the direction and size of the weld meet the requirements of the engineering specifications. If there are irregular welds, methods such as sand blasting and chemical cleaning can be used to remove the weld seams.
(2) Non-destructive testing
Non-destructive testing refers to the use of heat, sound, light, electricity and magnetism caused by abnormal internal structure or defects of the material on the premise of inspecting the inside of mechanical materials without damaging or affecting the performance of the object being tested and without damaging the internal organization of the object being tested. and other reaction changes, using physical or chemical methods as a means, and with the help of modern technology and equipment, to analyze the structure and state of the specimen's interior and surface, as well as the type, quantity, shape, nature, location, size, distribution and changes of defects. Methods for conducting inspections and tests. High-precision non-destructive testing technologies such as ultrasonic testing, X-ray testing or magnetic particle testing are used to detect possible defects in the welds. Once discovered, they need to be corrected in time.
(3) Mechanical parameter detection
Standardized testing equipment is used to measure the mechanical properties of electric welded steel pipes from multiple angles to determine whether they meet engineering requirements and standards. Commonly used mechanical property indicators include: strength, plasticity, hardness, impact toughness, fatigue strength, etc.
I believe that through the above introduction and acceptance methods, everyone has a certain understanding of the acceptance of welded steel pipes. During the process, we should be strict about the welding process and always put safety first. At the same time, we should also actively cooperate to carry out acceptance work as early as possible, detect and correct possible defects in a timely manner, and ensure the quality of steel pipe welding and the progress of project construction.
Previous:Steel well casing pipe sizes