Welded tubes are an integral component in various industries, serving as crucial elements in structural applications, machinery, and general manufacturing processes. The American Society for Testing and Materials (ASTM) has established standards for welded tubes to ensure consistency, quality, and safety across different applications. In this comprehensive guide, we will delve into the significance of ASTM sizes for welded tubes, exploring the standards, specifications, and considerations essential for understanding and selecting the right welded tube sizes for specific needs.
1.Importance of ASTM Standards for Welded Tubes
(1)Ensuring Structural Integrity
ASTM standards for welded tubes are designed to guarantee the structural integrity of these components. By specifying dimensions, tolerances, and material requirements, these standards help manufacturers produce welded tubes that meet stringent performance criteria, contributing to the overall safety and reliability of structures and machinery where these tubes are utilized.
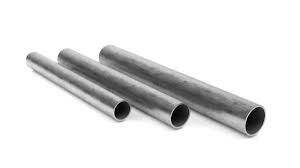
(2)Quality Assurance
Adherence to ASTM sizes and standards is a testament to the quality of welded tubes. Compliance with these specifications ensures that the tubes possess the necessary mechanical properties and dimensional accuracy, enabling them to perform as intended under various loads and environmental conditions.
(3)Interchangeability and Compatibility
Standardized ASTM sizes enable interchangeability and compatibility across different products and systems. This uniformity is particularly crucial in industries where welded tubes are used in conjunction with other components, ensuring seamless integration and consistent performance.
2.Overview of ASTM Sizes for Welded Tubes
(1)Dimensions and Tolerances
ASTM sizes for welded tubes encompass a range of dimensions and tolerances to accommodate diverse application requirements. These specifications cover parameters such as outside diameter, wall thickness, and length, providing a comprehensive framework for manufacturers and users to select the most suitable welded tube sizes for their specific needs.
(2)Classification by Shape and Application
Welded tubes are classified based on their shapes and applications, with ASTM standards offering distinct size ranges for round, square, rectangular, and special-shaped tubes. This categorization facilitates targeted selection based on the intended use of the welded tubes, allowing for precise matching of size and form to the demands of the application.
(3)Material Specifications
In addition to dimensional requirements, ASTM sizes for welded tubes include material specifications, encompassing the types of steel, alloy compositions, and surface finishes permitted for use in the production of these tubes. These specifications ensure that the materials used in welded tube manufacturing meet the necessary strength, corrosion resistance, and other mechanical properties required for their intended applications.
3.Considerations for Selecting ASTM Sizes for Welded Tubes
(1)Application-Specific Requirements
When choosing ASTM sizes for welded tubes, it is essential to consider the specific requirements of the application. Factors such as load-bearing capacity, environmental exposure, and compatibility with other components should inform the selection of welded tube sizes to ensure optimal performance and longevity.
(2)Regulatory Compliance
Certain industries and applications are subject to regulatory standards and codes that mandate the use of ASTM-compliant welded tubes. It is imperative to verify the applicable regulations and ensure that the selected tube sizes adhere to the necessary ASTM standards to maintain compliance and uphold industry best practices.
(3)Manufacturing and Fabrication Considerations
Manufacturers and fabricators must consider the feasibility of producing welded tubes in accordance with ASTM sizes, taking into account production capabilities, material availability, and welding processes. Adhering to ASTM standards may necessitate specific manufacturing techniques and quality control measures to meet the prescribed size and quality requirements.
Conclusion
ASTM sizes for welded tubes play a pivotal role in standardizing the dimensions, tolerances, and material specifications of these critical components. By adhering to these standards, manufacturers can produce welded tubes that offer reliable performance, structural integrity, and compatibility with a wide array of applications. Furthermore, users can confidently select ASTM-compliant welded tube sizes knowing that they meet rigorous quality and safety criteria.
1.Importance of ASTM Standards for Welded Tubes
(1)Ensuring Structural Integrity
ASTM standards for welded tubes are designed to guarantee the structural integrity of these components. By specifying dimensions, tolerances, and material requirements, these standards help manufacturers produce welded tubes that meet stringent performance criteria, contributing to the overall safety and reliability of structures and machinery where these tubes are utilized.
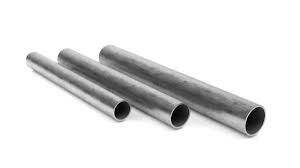
(2)Quality Assurance
Adherence to ASTM sizes and standards is a testament to the quality of welded tubes. Compliance with these specifications ensures that the tubes possess the necessary mechanical properties and dimensional accuracy, enabling them to perform as intended under various loads and environmental conditions.
(3)Interchangeability and Compatibility
Standardized ASTM sizes enable interchangeability and compatibility across different products and systems. This uniformity is particularly crucial in industries where welded tubes are used in conjunction with other components, ensuring seamless integration and consistent performance.
2.Overview of ASTM Sizes for Welded Tubes
(1)Dimensions and Tolerances
ASTM sizes for welded tubes encompass a range of dimensions and tolerances to accommodate diverse application requirements. These specifications cover parameters such as outside diameter, wall thickness, and length, providing a comprehensive framework for manufacturers and users to select the most suitable welded tube sizes for their specific needs.
(2)Classification by Shape and Application
Welded tubes are classified based on their shapes and applications, with ASTM standards offering distinct size ranges for round, square, rectangular, and special-shaped tubes. This categorization facilitates targeted selection based on the intended use of the welded tubes, allowing for precise matching of size and form to the demands of the application.
(3)Material Specifications
In addition to dimensional requirements, ASTM sizes for welded tubes include material specifications, encompassing the types of steel, alloy compositions, and surface finishes permitted for use in the production of these tubes. These specifications ensure that the materials used in welded tube manufacturing meet the necessary strength, corrosion resistance, and other mechanical properties required for their intended applications.
3.Considerations for Selecting ASTM Sizes for Welded Tubes
(1)Application-Specific Requirements
When choosing ASTM sizes for welded tubes, it is essential to consider the specific requirements of the application. Factors such as load-bearing capacity, environmental exposure, and compatibility with other components should inform the selection of welded tube sizes to ensure optimal performance and longevity.
(2)Regulatory Compliance
Certain industries and applications are subject to regulatory standards and codes that mandate the use of ASTM-compliant welded tubes. It is imperative to verify the applicable regulations and ensure that the selected tube sizes adhere to the necessary ASTM standards to maintain compliance and uphold industry best practices.
(3)Manufacturing and Fabrication Considerations
Manufacturers and fabricators must consider the feasibility of producing welded tubes in accordance with ASTM sizes, taking into account production capabilities, material availability, and welding processes. Adhering to ASTM standards may necessitate specific manufacturing techniques and quality control measures to meet the prescribed size and quality requirements.
Conclusion
ASTM sizes for welded tubes play a pivotal role in standardizing the dimensions, tolerances, and material specifications of these critical components. By adhering to these standards, manufacturers can produce welded tubes that offer reliable performance, structural integrity, and compatibility with a wide array of applications. Furthermore, users can confidently select ASTM-compliant welded tube sizes knowing that they meet rigorous quality and safety criteria.
Previous:Acceptance criteria for welded tubes