Carbon steel plate: the basic material of the industrial backbone
Carbon steel plates, as an indispensable basic material in the industrial field, are everywhere. It is made of plain carbon steel or carbon steel with a carbon content of less than 2.11%, and no metal elements are deliberately added. In addition to carbon, it also contains a small amount of sulfur, silicon, phosphorus, manganese and other elements. Due to its good comprehensive performance and relatively affordable cost, carbon steel plates are used in the construction field to build stable steel structure frames and provide solid support for high-rise buildings. In the machinery manufacturing industry, it is the key raw material for manufacturing various mechanical parts. From precision small components to large mechanical structural parts, carbon steel plates are indispensable.
Iron smelting: The beginning of everything
The source of carbon steel plate manufacturing is to extract iron from iron ore. After the iron ore is mined, it contains impurities and needs to be crushed and beneficiated first. The selected iron ore is fed into the blast furnace together with coke, limestone and other raw materials. When the reaction inside the furnace is fully carried out, the molten iron, in a liquid state at high temperatures, flows out from the bottom of the blast furnace, completing the magnificent transformation from ore to iron and laying the foundation for the subsequent steelmaking process.
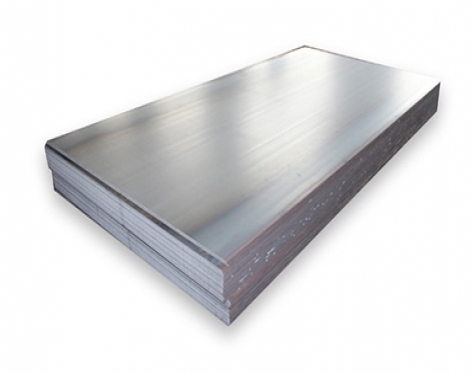
Steelmaking: Removal of impurities and blending of elements
Although the molten iron flowing out of the blast furnace has been initially formed, it cannot be directly used to manufacture carbon steel plates and needs to be further refined into steel. Converter steelmaking is a common method, where molten iron is poured into the converter and oxygen is blown in from the top. Oxygen acts like a "cleaner", rapidly undergoing a violent oxidation reaction with impurities such as carbon, silicon, manganese, and phosphorus in the molten iron.
Taking the reaction of carbon and oxygen as an example, carbon monoxide gas will be generated and discharged, effectively reducing the carbon content. A large amount of heat will be released during the reaction, causing the temperature in the furnace to soar to around 1600°C, which is why converter steelmaking does not require additional heating. In order to better remove impurities such as phosphorus and sulfur, slag-making materials such as lime need to be added. After these slag-making materials react with impurities, slag will be formed and float on the surface of the molten steel, which is easy to separate.
Continuous casting or rolling: giving shape
The refined molten steel has an extremely high temperature and good fluidity, like a long, hot silver river, providing the basic conditions for subsequent forming processing. At this point, it is fed into a continuous casting machine or rolling mill. The crystallizer of the continuous casting machine is the key part. It is like a precise mold, in which the molten steel cools rapidly, gradually changing from liquid to solid to form continuous ingots. The continuous rolling mill further processes the ingot through continuous rolling with multiple rolls.
Heat treatment: performance enhancement
Carbon steel plates formed by continuous casting or continuous rolling need to be heat treated to further improve their performance. Heat treatment is the process of changing the internal structure of metals through heating, insulation and cooling to obtain the desired properties.
Normalizing is a common heat treatment process, which heats the steel plate to 30-50℃ above the critical temperature, keeps it at that temperature for a period of time and then cools it in air.
Quenching is to heat the steel plate to above the critical temperature, keep it warm, and then quickly put it into the cooling medium for rapid cooling. The cooling rate needs to be greater than the critical cooling rate to obtain the martensitic structure and significantly improve the hardness and wear resistance. However, the steel plate after quenching is more brittle and has greater internal stress, so it needs to be tempered in time.
Tempering is the process of heating the quenched steel plate to below the critical temperature, keeping it warm and then cooling it. Low temperature tempering (150 - 250℃) can reduce internal stress and maintain high hardness, and is often used for cutting tools and measuring tools; Medium temperature tempering (350 - 500℃) can obtain good elasticity, suitable for parts such as springs; High temperature tempering (500 - 650℃) can make the steel plate have both strength, hardness and toughness, such as shafts, gears and other important parts;
Surface treatment: protection and beautification
Spraying is a common surface treatment method. In the production of some mechanical housings, the carbon steel plate surface is first cleaned to remove impurities such as oil and dust, and then electrostatic spraying technology is used to evenly spray powder coating on the steel plate surface.
Galvanizing is also a common method, which is divided into hot-dip galvanizing and electro-galvanizing. During hot-dip galvanizing, the carbon steel plate is immersed in molten zinc liquid, and the surface of the steel plate will quickly react with the zinc to form a zinc-iron alloy layer and a pure zinc layer. The two layers of structure are closely combined, just like putting a layer of solid armor on the carbon steel plate, which can effectively prevent the steel plate from rusting and extend its service life.
Electro-galvanizing uses the principle of electrolysis to deposit a layer of zinc on the surface of carbon steel plates. The galvanized layer obtained by this method is more uniform and fine, and is suitable for products with high requirements on appearance, such as automotive parts and home appliance casings.
Chrome plating can also improve the surface properties of carbon steel plates. The chrome plating layer has high hardness, good wear resistance, and also has good chemical stability and decorative properties.
Read more: Density of Carbon Steel Plate and Influencing Factors
Carbon steel plates, as an indispensable basic material in the industrial field, are everywhere. It is made of plain carbon steel or carbon steel with a carbon content of less than 2.11%, and no metal elements are deliberately added. In addition to carbon, it also contains a small amount of sulfur, silicon, phosphorus, manganese and other elements. Due to its good comprehensive performance and relatively affordable cost, carbon steel plates are used in the construction field to build stable steel structure frames and provide solid support for high-rise buildings. In the machinery manufacturing industry, it is the key raw material for manufacturing various mechanical parts. From precision small components to large mechanical structural parts, carbon steel plates are indispensable.
Iron smelting: The beginning of everything
The source of carbon steel plate manufacturing is to extract iron from iron ore. After the iron ore is mined, it contains impurities and needs to be crushed and beneficiated first. The selected iron ore is fed into the blast furnace together with coke, limestone and other raw materials. When the reaction inside the furnace is fully carried out, the molten iron, in a liquid state at high temperatures, flows out from the bottom of the blast furnace, completing the magnificent transformation from ore to iron and laying the foundation for the subsequent steelmaking process.
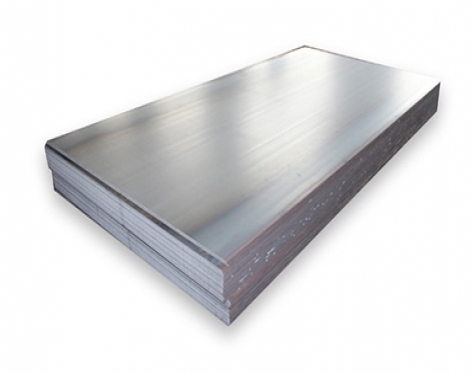
Steelmaking: Removal of impurities and blending of elements
Although the molten iron flowing out of the blast furnace has been initially formed, it cannot be directly used to manufacture carbon steel plates and needs to be further refined into steel. Converter steelmaking is a common method, where molten iron is poured into the converter and oxygen is blown in from the top. Oxygen acts like a "cleaner", rapidly undergoing a violent oxidation reaction with impurities such as carbon, silicon, manganese, and phosphorus in the molten iron.
Taking the reaction of carbon and oxygen as an example, carbon monoxide gas will be generated and discharged, effectively reducing the carbon content. A large amount of heat will be released during the reaction, causing the temperature in the furnace to soar to around 1600°C, which is why converter steelmaking does not require additional heating. In order to better remove impurities such as phosphorus and sulfur, slag-making materials such as lime need to be added. After these slag-making materials react with impurities, slag will be formed and float on the surface of the molten steel, which is easy to separate.
Continuous casting or rolling: giving shape
The refined molten steel has an extremely high temperature and good fluidity, like a long, hot silver river, providing the basic conditions for subsequent forming processing. At this point, it is fed into a continuous casting machine or rolling mill. The crystallizer of the continuous casting machine is the key part. It is like a precise mold, in which the molten steel cools rapidly, gradually changing from liquid to solid to form continuous ingots. The continuous rolling mill further processes the ingot through continuous rolling with multiple rolls.
Heat treatment: performance enhancement
Carbon steel plates formed by continuous casting or continuous rolling need to be heat treated to further improve their performance. Heat treatment is the process of changing the internal structure of metals through heating, insulation and cooling to obtain the desired properties.
Normalizing is a common heat treatment process, which heats the steel plate to 30-50℃ above the critical temperature, keeps it at that temperature for a period of time and then cools it in air.
Quenching is to heat the steel plate to above the critical temperature, keep it warm, and then quickly put it into the cooling medium for rapid cooling. The cooling rate needs to be greater than the critical cooling rate to obtain the martensitic structure and significantly improve the hardness and wear resistance. However, the steel plate after quenching is more brittle and has greater internal stress, so it needs to be tempered in time.
Tempering is the process of heating the quenched steel plate to below the critical temperature, keeping it warm and then cooling it. Low temperature tempering (150 - 250℃) can reduce internal stress and maintain high hardness, and is often used for cutting tools and measuring tools; Medium temperature tempering (350 - 500℃) can obtain good elasticity, suitable for parts such as springs; High temperature tempering (500 - 650℃) can make the steel plate have both strength, hardness and toughness, such as shafts, gears and other important parts;
Surface treatment: protection and beautification
Spraying is a common surface treatment method. In the production of some mechanical housings, the carbon steel plate surface is first cleaned to remove impurities such as oil and dust, and then electrostatic spraying technology is used to evenly spray powder coating on the steel plate surface.
Galvanizing is also a common method, which is divided into hot-dip galvanizing and electro-galvanizing. During hot-dip galvanizing, the carbon steel plate is immersed in molten zinc liquid, and the surface of the steel plate will quickly react with the zinc to form a zinc-iron alloy layer and a pure zinc layer. The two layers of structure are closely combined, just like putting a layer of solid armor on the carbon steel plate, which can effectively prevent the steel plate from rusting and extend its service life.
Electro-galvanizing uses the principle of electrolysis to deposit a layer of zinc on the surface of carbon steel plates. The galvanized layer obtained by this method is more uniform and fine, and is suitable for products with high requirements on appearance, such as automotive parts and home appliance casings.
Chrome plating can also improve the surface properties of carbon steel plates. The chrome plating layer has high hardness, good wear resistance, and also has good chemical stability and decorative properties.
Read more: Density of Carbon Steel Plate and Influencing Factors